Smarter, safer and more sustainable falsework and formwork solutions
June 10, 2024
Advancements such as BIM, prefabrication techniques, and the integration of automation are already enhancing efficiency, safety, and quality in construction processes. How are these being utilised in the industry?
With advancements in materials and technology, falsework and formwork systems have become more efficient, durable, and adaptable, meeting the evolving demands of modern construction projects.
Robert Hauser, CEO of Doka, understands that technology is the key to the future and the company is driving the development of innovative products and services for users in the industry.
Hauser says that digital tools such as BIM (Building Information Modelling) allow Doka to create 3D models for formwork, optimising material usage and thereby ensuring a perfect fit.
Doka is also optimising digital tools in the form of Concremote. The company’s concrete monitoring system uses sensors to measure the temperature and calculate the compressive strength of the concrete structure.
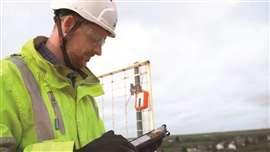
Concrete sensors
Also utilising concrete sensors is the construction company Costain. The company has been using Maturix’s concrete sensors to monitor the temperature and strength of setting concrete in formwork projects.
The technology has been implemented across several Costain projects in the road, water, and rail sectors.
The Gaia 200 sensors, which are as large as a smartphone, send real-time temperature and strength data wirelessly to engineers, temporary works designers, and other specialist contractors.
Costain says that the information can help users make faster and more informed decisions. For example, they can decide when to remove the formwork after a concrete pour.
On average, the introduction of these sensors is said to have reduced the time that formwork is in place by approximately 33%.
One Costain project has already used the sensors for more than 80 different pours and structures, eliminating the need to conduct destructive testing of approximately 500 strike cubes.
Bhavika Ramrakhyani, head of materials at Costain, commented, “We have an important role to play in maximising efficiency for our customers without compromising on quality or safety. It is important that our engineers have instant access to the right information at the right time, with crucial information sent directly to their devices and laptops.
“This means they can make informed decisions to accurately determine when it is safest to remove the temporary falsework and formwork after a pour.”
Ramrakhyani adds, “We’ve already seen enormous efficiency benefits. Programme delivery speeds have improved considerably, with striking times reduced by a third on sites where we have used the sensors.
“At the same time, the technology enables us to repurpose and reuse more of our temporary structures, as well as reducing the quantity of materials used, lowering our carbon footprint, which is another major benefit.”
Potential for innovation
Like Costain, Hauser recognises that there is immense potential for innovation to revolutionise the way formwork is manufactured and used on construction sites.
He adds that advancements such as BIM, prefabrication techniques, and the integration of automation already enhance efficiency, safety, and quality in construction processes and that we will see more of this in the future.
Attempting to drive new technology into the formwork industry are robotics company Saeki. The company’s robots make 3D-printed formwork to make non-standard and custom construction elements risk-free.
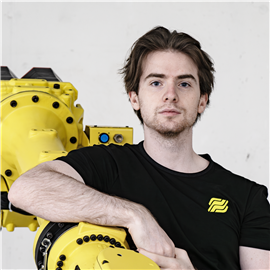
Saeki says that this provides a cost-effective, sustainable solution for low-volume production of non-standard concrete elements.
The startup currently operates with only two robots that work independently to create formwork. This formwork is shipped directly to construction companies to be used on construction sites or to manufacturers who pre-cast the concrete elements and sell them to contractors.
However, the company’s ultimate goal is not to act as a 3D printed formwork manufacturer, but rather to sell subscriptions to its services for 3D printing formwork and other components.
Under this business model, known as “robotics as a service”, Saeki plans to develop several 3D printing hubs, each consisting of at least 10 robots. This will allow customers from all over the world to book time with the robots to fulfil regular orders.
Andrea Perissinotto, one of the company’s co-founders, spoke to Construction Briefing. He says, that if 3D-printed formwork is adopted on a large scale, it has the potential to fundamentally change the construction and design process and reduce the amount of concrete used.
“Up to 80% of the materials used in a modern building do not need to be there,” Perissinotto says.
“There is no need to cast 30 centimetres of concrete all the way through a building, it’s just cheap to do it because concrete is cheap. By optimising the geometry of a building and the loads that go into it, you can take a lot of concrete out of the building.
“At the moment, these connection details are very expensive because if you create an optimised column, it’s going to have some sort of intricate details and it’s just cheaper to cast a thicker slab. But with 3D printed formwork, these geometrical limitations are not limitations anymore.”
Sustainable developments
Sustainability is also a key focus of the latest industry innovations, exemplified by the development of lightweight, reusable formwork systems that minimise waste and environmental impact.
For Doka’s Hauser, the future of scaffolding and formwork is about smarter, safer, and more sustainable solutions.
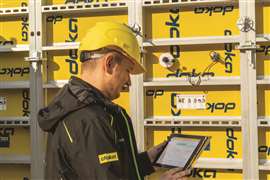
Sustainable solutions are taking centre stage for Doka as the company looks at the ways they can reduce emissions. Hauser highlights that the Austria-based company is using data-driven sustainability to measure the greenhouse gas (GHG) emissions generated by its products over the relevant material life cycle phases.
In this way, users can better understand their environmental impact and consider the options to reduce their emissions by selecting more environmentally friendly products and systems.
For Hauser and Doka, the ultimate goal is to create inherently sustainable products that are key to achieving the company’s net-zero emissions strategy by 2040.
He adds, “Advanced materials not only help make products more environmentally friendly but also improve handling through the use of lighter materials and improved safety features.”
There are many notable and exciting trends in sustainable construction at present but one that is standing out for Doka is reducing the environmental impact of concrete, especially its significant CO2 emissions.
Hauser says, “Its strength, durability, availability, and other attributes make it an indispensable building material in the construction industry for many years to come. Finding new ways to make building with concrete more sustainable will require the serious attention of all the players in our industry.”
Low-carbon concrete
A promising option, says Hauser, is the use of low-carbon concrete mixes, which use less clinker content but come with prolonged curing times, particularly in colder climates.
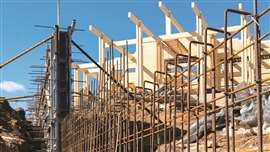
“This extended curing period poses real-world cost and efficiency challenges, as it affects project timelines and requires that formwork remain in place for longer periods.
“Recent collaborative research projects with industry leaders such as Strabag and Holcim in Austria seek to develop solutions that maintain the performance standards of low-carbon concrete.”
Doka’s contribution to projects like these includes the development of an intelligent heated formwork prototype aimed at expediting early strength development and facilitating the practical implementation of CO2-reduced concrete.
“This includes the use of more sustainable materials, waste reduction, the circular economy and minimising the carbon footprint of construction projects,” says Hauser.
“Many of the solutions we need to get to net zero already exist, but others need to be explored and innovated. This is where the greatest potential lies: in understanding sustainability as a catalyst for the development of new business models, products or services.”
In agreement with Hauser, it is clear that the industry has the opportunity to lead by example in adopting environmentally friendly practices for the future of falsework and formwork.
STAY CONNECTED



Receive the information you need when you need it through our world-leading magazines, newsletters and daily briefings.
CONNECT WITH THE TEAM



