Looking up: Global high-rise construction trends
April 26, 2024
Worries over financing, liquidity in some regions, and meeting sustainability seem to be lessening as the planet’s urban centres keep building into the sky, Mitchell Keller reports.
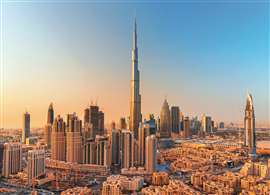
As much as times have changed, some things need to stay the same.
In the high-rise construction segment – from formwork/falsework to tower cranes and new technology – modernisation has been incremental, but that should probably be expected from a section of the industry that has always required utilising the best advanced methods to an efficient end.
So, where has high-rise construction changed? In the details.
Whether it is companies turning to virtual reality or modelling scanning, perfecting autonomous platforms, lifts, and cranes, or simply embracing collaboration through digital tools, the nearly 140-year-old practice of building high-rises is as exciting as ever.
Riyadh’s 2km supertall
Announced in late 2022, Saudi Arabia’s capital city of Riyadh is planning to make room for an astonishingly massive 2,000m-tall (6,562-ft-tall) tower, which would surpass the current world’s tallest building (United Arab Emirate’s Burj Khalifa in Dubai) by more than 1km; Burj Khalifa is 828m-tall (2,717-ft-tall).
Architects’ Journal in London reported in March 2024 that UK-based architecture firm Foster + Partners was working on the multi-billion-dollar project.
No designs have yet emerged nor has the scheme been publicly approved or financed, but if construction gets underway, this one will be hard to miss in Riyadh; the current tallest tower in the Saudi Arabia capital is the PIF Tower at 385m (1,263 ft).
Elsewhere, the US State of Oklahoma is ranked 34th among the country’s 50 states for overall population density but that hasn’t stopped its largest city, and capital, Oklahoma City, from planning to build the country’s (and continent’s) largest tower.
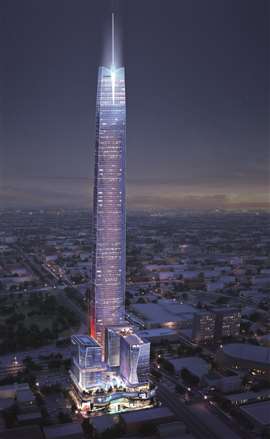
The Boardwalk at Bricktown is a major construction project in Oklahoma City that seeks to add residential and resort dwelling along with entertainment venues to the city’s centre. The plan includes constructing three towers at approximately 107m (350 ft) and a fourth nearly 600m tall (nearly 2,000-ft-tall).
Originally, a tower shorter than the country’s current leader (One World Trade Center in New York City), was proposed at 533m (1,750 ft), but an announcement by the project developer in January said a new scheme to erect a 581m (1,907 ft), 134-storey skyscraper had, allegedly, received full financing of roughly US$1.5 billion.
Speculation has abounded on the feasibility and practically of such a build. Critics have suggested that construction to its full height is unlikely.
Regardless, the Boardwalk at Bricktown will get built, even if at a reduced capacity. If the 1,907 ft and 1,750 ft towers are denied, the project will go forward with a complex of four towers of approximately 350 ft (107m) each.
China’s supertall supremacy
Until recently, China outpaced all countries when it comes to supertall buildings, with more than 3,000 buildings taller than 150m – the next closest country is the US with approximately 900. Liquidity issues and allegations of illegally obtained building permits by China-based real estate developer Evergrande, as well as a cap on the height of skycrapers of 500m introduced in 2021 has dampened the appetite for statement supertall buildings in the country. But several high-profile projects are still ongoing.
Set to open this year is the International Land-Sea Center in Chongqing, China. It topped out in late 2022. The 458m-tall structure was designed by KPF (Kohn Pedersen Fox Associates) and is the anchor of a three-building complex in southwest China.
China Construction Third Engineering Bureau Co served as main contractor with Arup working as structural engineer on the concrete-steel composite building.
In Nanjing, two towers of comparable height are currently under construction with plans to open in 2025. The shorter of the two, the HeXi Yuzui Tower A, is expected to reach a height of 498.8m (1,636 ft). The office building will be just one metre shorter than the Greenland Jinmao International Financial Centre (499.9m), which will be nearby Tower A.
Tower A was designed by Adrian Smith + Gordon Gill Architecture and is being constructed by main contractor Nanjing Runmao Real Estate Co. Its design will feature a 360-degree open-air observatory at the top, which will be one of the highest on the planet.
The Greenland Jinmao supertall was designed by Skidmore, Owings & Merrill (SOM), which is also acting as structural and MEP engineer. Greenland Group is serving as developer.
Electrifying tower cranes
Arguably one of the biggest changes in recent years in high-rise construction is the reliability and accessibility of all-electric tower cranes. While most modern tower cranes have been manufactured to run on electricity since the 1970s, their high-power demand can make it difficult for contractors to connect directly to national or municipal grids.
In recent years, though, advancement in electrification and the introduction of novel alternative fuel sources has made the possibility of using non-diesel power more plausible for contractors.
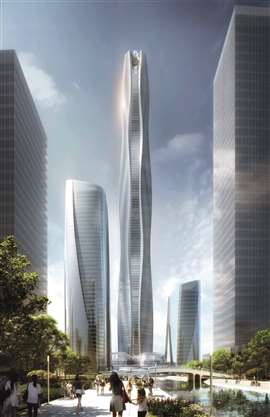
This March, US-based United Rentals, the world’s largest equipment rental company, introduced battery-energy systems for tower cranes for the first time to the North American market.
“Configurable up to 500kW, the system operates alongside a generator to deliver reliable power to support tower crane operations,” said United Rentals. “It minimises generator run time by storing energy in batteries and running on battery power whenever possible.”
For smaller operations, the system can run entirely ‘emission-free’ with solar-generated power.
Termaco, a Canada-based designer, manufacturer, and integrator of advanced solutions for the protection of energy storage systems, developed the energy system in partnership with United for an Edmonton, Canada, jobsite.
The project was for a 20-acre mixed-used community, and it used an eight-ton, 70-metre-tall tower crane, which was fully-powered by the Termaco energy system.
“At the project, [the contractor] went from running a 300kVA T4 generator 24-hours a day to power its tower crane, to charging the battery energy system with a 100kW generator for just two-and-a-half hours a day and operating the crane solely on battery power,” said United.
The company said, for this project, generator runtime was reduced by 91%, which resulted in an estimated 80% reduction of fuel and emissions.
However, electrified tower cranes aren’t just getting more efficient and reliable; they’re also getting bigger.
In October 2023, Mammoet – a Dutch heavy lifting and transport solution company – announced a major construction milestone for what it called the ‘world’s largest’ and highest-capacity electric crane: the SK6000.
The electric tower-crane model has been in-development for years but is expected to be released in 2024. The numerical figure in its name represents its 6,000-tonne capacity.
Mammoet launched the new product with module lifting in mind. The crane is intended to lift 3,000-tonne components at a 220m hook-height with a 144m maximum radius. The company said the unit will be able to lift modules in the 3,000- to 6,000-tonne range.
Towering over the competition
Most buildings aren’t constructed to win awards, but occasionally a scheme captures the imagination of the public and trade organisations, and some project leaders get to go home with more hardware than just their machines and tools.
One such structure and project is Denmark’s Lighthouse 2.0 in the city of Aarhus. Located in the Aarhus Docklands, the 44-floor, 142m (466 ft) residential building is the country’s largest of its type. Completed in 2022, it created 381 new dwellings less than 3km (1.9 mi) from the city’s centre.
Late in 2023, the US-based Council on Tall Buildings and Urban Habitat (CTBUH) – an international body that studies and reports on planning, design, and construction of tall buildings – bestowed Lighthouse 2.0 with the award for Best Tall Building in the 100m to 199m category.
The design features approximately 20,000m2 of double-glazing glass, with a base-structure made mostly of concrete. At the ground level, the tower is surrounded by tiered plazas of indoor and outdoor spaces.
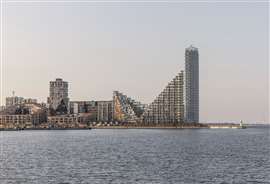
The materials, specific geometry, and tight location near the sea required close collaboration between the project’s general contractor and Germany-based Peri – the Lighthouse 2.0 formwork and scaffolding supplier.
“The special architectural requirements and the demanding construction schedule called for close cooperation between general contractor Per Aarsleff A/S and Peri,” remarked Peri.
Peri’s ACS self-climbing system was used on the project, which the company said features a high-capacity single stroke cylinder that climbs to the next level in only 20 minutes using less brackets, anchors, and overall parts and pieces than older self-climbing units.
Designed for the US markets, Peri noted use of the ACS on the Lighthouse project was a first in Denmark.
“The rail-guided climbing formwork impressed with its hydraulic drive, large climbing units, high lifting force and fast processes,” said Peri, adding it’s ACS Core 400 unit, in particular, is adept at supporting concrete placing booms, which was ideal for this concrete-centric project.
“This meant that a concreting cycle of just one week per floor could be realised,” explained the company.
Due to the building’s plaza design, the crowning of the structure required a customised solution before it could be completed.
“The challenge lay in the fact that the geometry of the upper floors differed from that of the lower floors,” explained Peri. “It would not have been profitable to erect scaffolding up to the [top] floor, so a completely new approach to scaffolding construction had to be found.”
Aarsleff’s site manager, Jesper Scharff Lanng, notes that top-floor panoramic windows, a 44th-floor restaurant, and the roof terrace design called for an “innovative custom solution.”
Engineers put in more than 400 work hours to create the solution, which involved erecting 50 tonnes of scaffolding, some of which was installed on the interior as well as exterior.
Lanng noted, “Erecting scaffolding inside the building that extends to the outside is nothing unusual, but if you’re installing 50 tonnes of scaffolding across four storeys on the 43rd floor, then that’s a different ball game.”
Safety emphasis
A high-rise can’t touch the sky without first building its foundation and support, and the role of formwork and cranes in the modern era is about utilising tried-and-true methods while innovating mechanics to increase productivity.
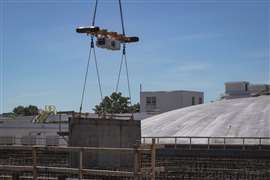
While formwork providers are increasingly adopting new technologies like 3D-scanning, 4D-planning, and incorporating BIM (building information modelling) and digital twin capabilities into their services, perhaps the biggest emphasis in the sector is on safety.
Steve Duthie, an associate director with Altrad RMD Kwikform, said the internal and external pressure to make construction sites safer is driving new products.
“When considering the sheer scale of a project, tight timeframes and the number of sub-contractors and teams all working under this kind of pressure, it is clear to see how potential safety risks can arise,” said Duthie.
RMD Kwikform’s Alshore Plus, a high-strength aluminium shoring system, is an example of conventional formwork products making safety-based improvements. It features a quick strike integral load release mechanism with tailored connections between frames and legs. The design, said RMD Kwikform, makes for faster installation time.
A quicker assembly means less people on-site for less time, but the Alshore Plus also improved ladder access, platforms, board bearers, and handrails throughout the system.
But even some of the simplest products, like RMD Kwikform’s Ascent-S safety screen and debris protection system, can make safer even the tightest of high-rise projects. The Ascent-S can come with different options of sheeting to curtail to the environment. A complete perimeter seal is also achievable, and all panels can be delivered pre-assembled to the site.
Another product in tower cranes aiding safety and improving efficiency is the Vita Load Navigator made by US-based Vita Industrial. It’s an application that goes on a tower crane hook to help stabilise materials, using a remote control, amid movement or in windy conditions.
It’s a tool Trent Johnson, district manager in the US Upper Midwest with PCL Construction, said his team has relied on for recent projects.
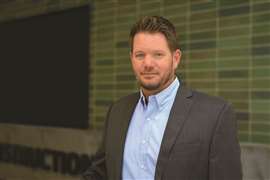
He said the original application was for military-based uses and applied the illustration of a rescue team removing someone from a remote situation.
“When they have to go in to save people, they send down the man, the basket, and put the person in there, but when they’re hoisting it back up, the helicopter blades would create turbulence and it would spin it,” said Johnson, noting that something similar can happen when large walls or wide materials are placed at height with a tower crane.
“These two pieces on the end are two fans that are run by a battery system,” said Johnson of the Vita Load Navigator. “With tower cranes and falsework and formwork, as you elevate it… the wind is hitting that formwork.”
Johnson said it can create a ‘pretty big sail’ and means that wind at 22 miles-per-hour (35km-per-hour) usually results in a non-workday for safety concerns.
The Vita Load Navigator reduces how much wind the material catches by blowing the material in resistance to the wind, making for more stable movement and placement.
“This piece of equipment allows us to work in high-wind environments,” said Johnson, who said one labourer would work in tandem with the crane operator to ensure a flush placement. “And, as [the crane operator is] dropping it, that’s when the guy that’s running the Vita Load Navigator will be able to dial in perfectly – within one to two degrees – of where it needs to go.”
While contractors, developers, and financers have certainly been disadvantaged by ballooning material costs, labour shortages, and inconsistent regulation on sustainability, there is little evidence that the public or developer’s appetite for big buildings is waning.
As long as giant builds can remain profitable and the world’s cities can benefit from immense towers, the same tantalising question will remain year-in-and-out: just how high in the sky can we go?
STAY CONNECTED



Receive the information you need when you need it through our world-leading magazines, newsletters and daily briefings.
CONNECT WITH THE TEAM



