Lithium battery recycling: where does the industry stand?
26 June 2023
In the second part of this article on various aspects of lithium battery recycling, Flash Battery, Italy-based manufacturer of lithium batteries for industrial machines and electric vehicles, helps us understand available recycling processes and future options such as direct recycling and second life for batteries.
How does the recycling process of a lithium battery currently work?
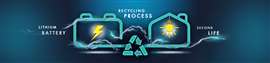
In part one of this article, we have already discussed the structure of a lithium battery and the current legislation regulating the recycling and disposal of lithium batteries in Europe, an area that is increasingly paving the way toward creating its own battery value chain. Now let us delve into the more technical aspects related to the current and future recycling processes.
Today, lithium battery recycling consists in multiple processing steps, which can be divided into two main types:
1. Physical processes
These include the disassembly, separation and shredding of the lithium battery components; they mainly serve as a pre-treatment to separate cathode and anode materials from other components such as current collectors and electrolytes, thereby reducing impurities and facilitating the following recovery processes.
2. Chemical processes
These include chemical precipitation, acid leaching, solvent extractions, electro depositions and smelting. These processes can in turn be divided into sub-categories:
- Pyrometallurgical processes
The most common as they are simple and productive, suitable for the recovery of the battery’s metallic materials but not for organic materials. These are high temperature processes (800-1300° C) that melt the different metals allowing their recovery in the form of alloys (copper, cobalt, nickel and iron). They are then further refined to obtain purer metal alloys.
Lithium, aluminium, silicon, calcium and manganese can instead be obtained from the slag, but with generally expensive processes. As a result, slag is often preferred to be used as a material for the construction industry. - Hydrometallurgical processes
These involve extraction, dissolution and separation of battery materials at low temperatures by chemical reactions in aqueous solutions. These processes are considered more sustainable and energy-efficient than pyrometallurgical ones but they are more complex as they require multiple steps. Recycling processes and schemes (from EU’s Battery 2030, see: https://battery2030.eu/digitalAssets/815/c_815818-l_1-k_battery-2030_roadmap-v2.1.pdf)
The seven steps driving the process of battery recycling
There are then seven fundamental phases to recycling, dependant on the complexity of the lithium cells (chemical and mechanical) and the recycling strategies of the different plants:
Preselection: the batteries are separated according to the different chemical and mechanical/geometric characteristics
Energy recovery: large cells/batteries can be subjected to a discharge process to recover the residual energy in them and to reduce the risks during disposal
Disassembly: creates metal, plastic and electronic components that can follow independent recycling processes
Decontamination: avoids the release of harmful emissions or hazardous materials into the environment.
Liberation: in which there is the detachment of the anode and cathode active materials from the metal current collectors. To this end, mechanical, thermal and chemical methods in inert atmosphere or aqueous solutions are used to decompose the metal binders and/or collectors.
Separation: the released materials are separated using different physicochemical properties (density, magnetic, electrostatic and geometric properties). However, amalgams are obtained which must be metallurgically refined to obtain components with greater purity.
Metallurgical refining: this can be thermal (pyrometallurgical processes), chemical (hydrometallurgical processes) or even biological (bio metallurgical).
The future of recycling is Direct Recycling
The recycling process is currently structured to obtain the basic elements and compounds used to synthesise the active materials, passing through the “black mass”, that is a pulp of cathode and anode materials still to be refined, with consequent waste of energy and other materials.
To make lithium battery recycling more efficient, next goal is direct recycling, in which the active materials are directly recycled as much as possible, rather than being transformed into black mass.
Collection systems based on the health of the modules and cells should also be introduced to facilitate and speed up the selection phase.
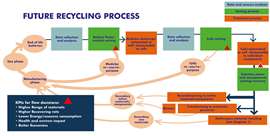
An interesting point is also the concept of “design for recycling” that means the mechanical design of the battery will be done considering from the outset the dismantling that will take place at the end of its life.
The active materials will then be recovered and regenerated as much as possible (secondary active materials) while, unlike current recycling, only the non-regenerable part will follow the transformation process into primary components (secondary raw materials). Both the first and the last can then re-enter the new cell production cycle and start the cycle over again.
It is important that the processes are all the more efficient when the initial material to be recycled is selected and with a very precise chemistry, thus it is necessary to improve the traceability of the cells, through label, RFID or similar applications, which uniquely identify their composition and the state of life for any second-life uses. Added to this is the challenge of finding convenient recycling processes given the constant decrease in cell costs due to increasingly high production.
The second life of lithium batteries: when is it possible?
More studies are also being carried out for giving a second life to lithium batteries after the end of their life in vehicles.
Giving a battery a second life means re- using a battery that has reached the end of its life for an electric vehicle, in other applications such as energy storage.
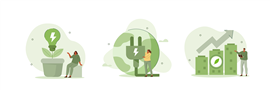
For example, an electric vehicle battery is said to be at the end of its life and ready for retirement when it loses 20% of its original capacity. However, there’s still residual energy in the battery that can be used for other applications that do not require its full capacity and can harness the remaining portion of energy that would otherwise go to waste. This operation not only extends the total lifespan of the battery, but also reduces the environmental impact of its production, recycling and disposal.
Depending on the type of use, the second life of a battery can last even more than 10 years.
End-of-life lithium batteries can be used, for example, to power utilities in houses and buildings. In fact, functioning of the electricity grid can be improved and, at the same time, greater use of the energy coming from renewable power plants can be made by providing an energy storage system or a system that reduces peak use of the national electricity grid through peak shaving, whereby the battery charges when there are production peaks and provide energy when it’s needed the most.
Second life however is an option that can be combined with recycling but cannot replace it, simply because it is applicable to limited sectors.
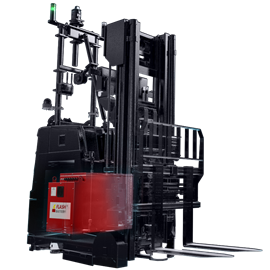
As a matter of fact, although very interesting, the second life concept is not always the best choice, especially in the industrial sector. In fact, many battery applications for industrial uses (e.g., logistics) can fully exploit the battery energy: thanks to the possibility of partial charging during breaks, these vehicles continue to use the battery up to a remaining capacity below 40% and consequently the second life is not necessary.
Another important reason that makes second life concept hard to apply in the industrial sector is the fact that models and battery packs are extremely different from one another and usually not produced in large volumes. Therefore, unlike for automotive lithium batteries, providing uniform re-assembly is very complex.
Sustainability and recycling at the heart of Flash Battery’s choices
Environmental awareness and recycling are the cornerstones of Flash Battery’s corporate vision: its goal ever since the company’s inception has been to make room for sustainable innovation in the industrial machines and electric vehicle market.
“Research and development and the implementation of increasingly streamlined processes to facilitate the recycling and recovery of a battery’s components are among the main goals of the European Green Deal and of all those manufacturers who, like us, want to play an active role in the creation of a European lithium battery value chain,” said Marco Righi, Founder and CEO of Flash Battery. “We keep a steady gaze on an ever-more sustainable future and anticipate European demands and regulations by continuously investing in research into efficiency- and sustainability-oriented materials and skills. As a result, the performance of the product is designed for compatibility with low environmental impact production processes where end-of-life battery disposal and recovery is a topic of focus.”
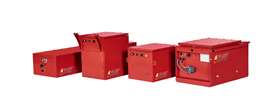
He added that Flash Battery is among the companies most involved in Europe’s largest electrification projects and partnerships, as shown by the membership to the Batteries European Partnership Association and the participation in projects such as the first IPCEI on Batteries, OPEVA, Thor, Fastest, and many more with the common goal of promoting sustainable development and optimization of electrification in Europe.
Flash Battery’s commitment to research, therefore, is not only limited to the product, but also contemplates the willingness to create synergies so that the entire sector can begin to produce in accordance with sustainability criteria by researching into more efficient and easily recycled materials.
The complete papers by Flash Battery on these topics can be found in the company’s blog.
STAY CONNECTED



Receive the information you need when you need it through our world-leading magazines, newsletters and daily briefings.
CONNECT WITH THE TEAM


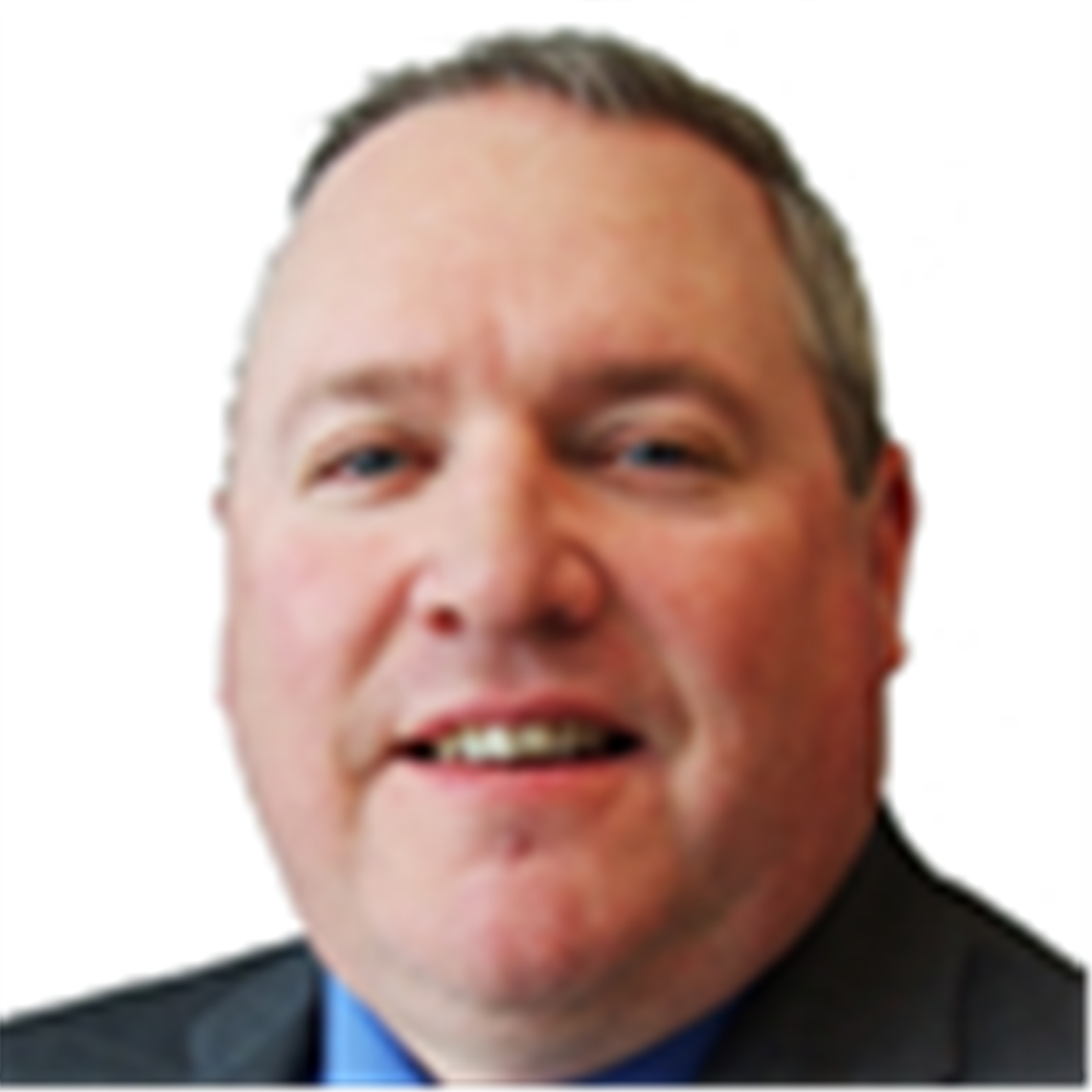
