‘There’s no path forward in construction without huge growth in modular’
21 October 2024
If you’ve ever been to Belgium’s capital Brussels, then there’s a chance you’ve ambled round the city’s opulent Grote Markt.
The square is flanked by a succession of beautiful buildings built painstakingly by craftsmen over hundreds of years, from the landmark Gothic Town Hall, to ornate Baroque guildhalls and the neo-Gothic King’s House.
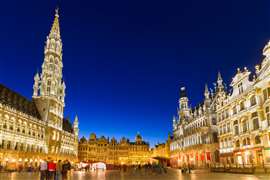
But just a few hundred metres away, around 200 people gathered earlier this month to discuss a very different and altogether more modern form of construction. It’s one that’s also arguably much less well loved, at least for now: modular.
World of Modular Europe was the first European event to be organised by the US-based Modular Building Institute since before the Covid pandemic.
The Modular Building Institute has around 650 members, most of which are based in North America, but a significant number of around 40 companies call Europe home.
Mirroring the larger, annual World of Modular, which attracts around 2,000 delegates from the industry, the Brussels event aimed to bring together not just manufacturers but contractors, engineers, architects, support companies, and developers and clients.
In doing so, Modular Building Europe hopes to foster better understanding of a corner of the building industry that offers a host of benefits and potential solutions to intractable problems like an ageing workforce, severely lagging productivity, pressure to reduce CO2 emissions, and a global housing shortage.
That better understanding is crucial because currently, for all its promise, modular construction is still failing to gain the sort of widespread adoption that many hoped it might have done by now.
‘The old-time ways of building seem to stick’
John Buongiorno started the modular division of New York-based Axis Construction, a construction management and general contracting firm, 25 years ago. Current board president of the Modular Building Institute and with 40 years’ experience in the industry, he knows more than most about the frustrations of wrestling modular into the mainstream.
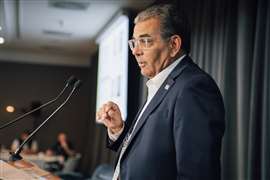
“We are a construction company specialising in healthcare. We do some very high-end, permanent healthcare structures including freestanding, multi-storey health clinics, full emergency rooms, extensions to existing hospitals, MRI buildings – just about anything healthcare related. The only thing we don’t do is residential,” he tells Construction Briefing.
“I’ve seen a lot of change in the industry but it’s very slow-moving. Certainly, by now I would have thought it would be a little bit more well received in the construction community. But, at least in the US, the old-time ways of building things seem to stick.”
Buongiorno suggests that fear of change is a major part of the challenge that modular faces but that once building owners and construction clients can see the benefits for themselves, their attitude shifts.
“Once we get in front of them and we show them the difference in schedule and quality, then they have that ‘ah-ha’ moment. They realise modular can look like a conventional building.”
Perception challenge
Changing perception, then, is a key part of the puzzle. In addition to overcoming the gradually fading preconception that modular means cheaply built, temporary structures, the number of high-profile failures in the sector presents a further risk to clients’ confidence - just this week, the UK has seen prominent modular company TopHat announce that it is winding down its factory operations amid a reduction in its future pipeline.
But Buongiorno feels there has been too much focus on failure of modular companies, given that insolvencies are a common occurrence across the construction industry as a whole. “If you are not funded properly, or you are not focused, or you have bad management, or take a scattergun approach, you are going to fail – that applies to any conventional construction business,” he contends.
“The failures this industry has seen come from a lack of knowledge of tying the design into the manufacturing and then the finishing on site,” says Buongiorno. “You can design anything you want and there’s going to be a factory to build the building. But then when it gets to site if the general contractor doesn’t know how to tie everything together then the project is going to be a failure.”
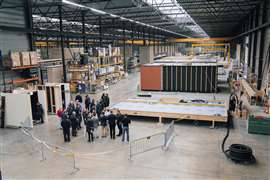
Modular’s potential
For his part, Modular Building Institute executive director Tom Hardiman is still a believer that modular is the way forward, in spite of its slow progress.
“I have staked my career on it,” he says. “I’ve been doing this for 20 years and it’s the potential [of modular] and the opportunity that drives me. Everything indicates that we need to move to a more industrialised process. There’s less labour available, there’s more demand on housing, costs are going up – we can’t keep building the way we have built.”
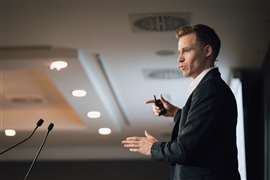
In the US, modular’s market share has tripled over the last seven years to 7%, Hardiman points out.
“We’re definitely growing. But it has been slower than I’d like and there are quite a few barriers,” he adds.
Modular’s potential is huge, as Erlend Spets, associate partner at McKinsey & Company, and a keynote speaker at the conference.
“In principle, modular can solve a lot of the challenges that construction sees,” said Spets, who also presented an early preview of an as-yet-unreleased McKinsey report on the modular sector.
“But it’s only at a fraction of its total potential.” Spets shared preliminary figures with the conference’s audience on just how large the global construction industry is today and how much of that figure is somehow addressable by modular. Unfortunately, those figures need to remain under wraps while they are finalised, but McKinsey estimates that it could be as much as half of the total.
Spets pointed to a recent McKinsey report on productivity in construction that shows how it has remained flat for many years. What little growth there has been largely came in China and Asia between 2010-20, while there has been a slight decline in Europe and a significant decline in the US over the past decade.
That leaves a huge gap in the requirement for construction capacity at a time when much of the industry’s labour force is starting to retire.
Modular, which Spets defined as construction that involves some kind of prefabrication, could help to solve not just the labour shortage, but also boost productivity, reduce cost, and reduce carbon emissions via better quality, more energy-efficient buildings and reduced waste.
Meanwhile, advances in technology are making it easier to design structures that incorporate modular elements in a more efficient way, rapidly changing configurations taking clients’ needs and local building codes into consideration, Spets says.
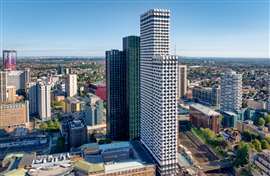
Shared experience
What strikes Hardiman is that no matter where delegates at the conference come from, whether it is the US, European Union, UK or even somewhere like Malaysia, the frustrations felt by modular construction professionals and the barriers are often the same.
“You can go anywhere in the world and talk to someone in the modular industry and pick up on similar themes,” he says. “It may be challenges with acceptance and the perception of the industry, getting through planning and permitting, approvals. You hear those common issues everywhere.”
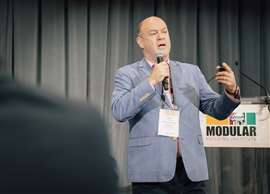
What a gathering like this can also uncover is examples of best practice that can be shared across borders, or even details of government-sponsored research projects whose findings can be of value in other markets, he argues.
“People don’t have to solve every problem themselves because normally someone else has already wrestled with it,” says Hardiman.
Meanwhile, Buongiorno has faith that modular will have its day. “It has taken a lot of work on our part to get the hospital systems in the New York area to understand the process and accept it and now believe in it.
“We’ve done four different projects for New York City. Breaking into that market is not easy – it’s probably the toughest market to build for in the country. But they see the speed and the quality.”
In the meantime, he wants to keep pushing for higher standards in the modular industry and working to amplify the message about modular’s potential benefits. “I want every project in our industry to be perfect because what happens then is it becomes more acceptable. As the delivery method becomes more successful and is promoted better, there’s going to be more opportunities. Then naturally, I am going to get more opportunities too.”
Hardiman expects modular’s market share to double again within the next five years in the US.
“All the signs we see are pointing upwards,” he says. “We have a massive housing shortage and labour shortage globally. Those things aren’t going to change in five years.”
Buongiorno concludes, “Once they have done a successful modular project, clients are not going to go back to building conventionally. I don’t think there is any path forward in construction without modular being a huge growth industry.”
MAGAZINE
NEWSLETTER
The gold standard in market research
Off-Highway Research offers a library of more than 200 regularly updated reports, providing forensic detail on key aspects of the construction equipment industry.
Our detailed insights and expert analyses are used by over 500 of the world’s largest and most successful suppliers, manufacturers and distributers, to inform their strategic plans and deliver profitable growth.