Has scaffold construction changed since the 1700s?
December 16, 2024
How does a scaffold do that – stand without collapsing under its own weight or from the loads that are applied to it? If you haven’t had the exhilarating experience of being on a scaffold several hundred feet above the ground, looking down a scaffold leg that is less than two inches in diameter, put it on your bucket list.
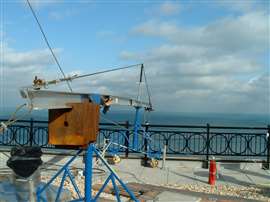
It’s magic that it can support any load. Why does a suspended scaffold hang there without falling? What’s the secret to the ability of these temporary structures to support substantial loads on such spindly legs and threadlike wires? While it’s a mystery to some, and perhaps a miracle to others, there is an explanation.
The idea that the strength of materials could be calculated was unknown for millennia. Construction was more art than science. Skilled craftsmen practiced their trade utilizing experience as a guide for future work. The great cathedrals of Europe are examples of this methodology where workers kept pushing the boundaries of knowledge by building bigger and bigger, stopping only when it was evident the structure they were constructing could no longer support the applied loads.
Supporting loads
It was only in the eighteenth century that science and mathematics developed to the extent that they could be used to accurately analyze and subsequently determine the ability of specific materials to resist forces and support loads. It was discovered during this time period that it was possible to create formulae that a designer could use to ascertain not only the strength of a certain material, such as iron, but also to determine what size a structural component needed to be to support a load. This knowledge created what is known as engineering and the practitioners of engineering utilize this created knowledge for design and analysis. In fact, this engineering knowledge is used to demonstrate how and why a scaffold can do what it does.
A column, such as a scaffold leg, can support a compressive load based on three factors: the type of material, the shape of the material, and the unbraced length of the column. For frame and system scaffolds, a round tube is the shape of choice. A round tube is used because it is equally strong in all directions, as compared to a rectangle for example, which is stronger in two directions and weaker in the other two directions. Square tubes, which minimize the difference, are the second choice and that is why you may see some scaffolding with square tubes. Why is a tube used instead of a solid rod? After all, a tree is solid.
Through research, it was determined that to achieve tube strength much more material was required around the outside perimeter of the tube than in the middle of the tube. Since the stuff in the middle of the tube wasn’t necessary it was removed. And that is why tubes are used instead of solid rods. Granted, a solid rod will support more load, but economics wins the day since tubes will produce satisfactory results. Besides, can you imagine the weight of a scaffold frame that had solid rods for legs?
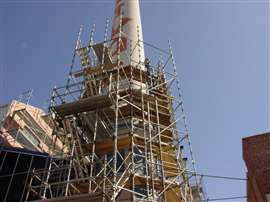
Changing shapes
Steel is the material of choice for most scaffolds. Early in the development of engineering, it was determined that the strength of a material varied greatly, based on the material mix, such as the ratio of carbon to iron ore. It was also determined that impurities were a bad thing. To achieve consistency, present day steel production is carefully controlled so that the material strength is very predictable and the scaffold manufacturer can thus produce a predictable product. Of course, on the other hand an unscrupulous manufacturer can use inferior steel but that is the subject for another time.
The third factor that determines the compressive strength of a column is the unbraced length. An unbraced 2-inch diameter tube is very strong in compression, but when it is 20 feet tall, it has no capacity at all. Leonhard Euler, a Swiss mathematician and physicist who lived in the eighteenth century, was the first to determine, in addition to the type of material and the shape of the column, that the unbraced length of the column was a significant factor in the strength of a column. He subsequently developed a formula that includes all three factors. In other words, his column formula, and others that followed, incorporate the relationship between shape, material strength and unbraced length. For scaffolding, the unbraced length is the vertical distance between horizontal members and the vertical distance between diagonal brace connections.
Scaffold erectors cannot change the material being used and cannot change the shape of the scaffold leg unless, of course, they used a kinked or bent tube. Using a bent or kinked tube is detrimental to the strength of the column and explains why damaged scaffold components should never be used. What scaffold erectors can do, and frequently do, is alter the unbraced length of the scaffold leg. The most common example is with frame scaffolds where the front crossbraces are never installed. This practice changes the unbraced length from four feet, the distance between crossbrace studs, to six and a half feet, the nominal height of a walk-thru frame. By doing so, the capacity of the scaffold leg is reduced by as much as fifty per cent. Conversely, increasing the number of horizontal members, and the correlating vertical diagonal braces, on a system scaffold so the unbraced length is reduced, significantly increases the capacity of the scaffold leg. Unfortunately, few are the erectors who understand the impact that bracing has on capacity.
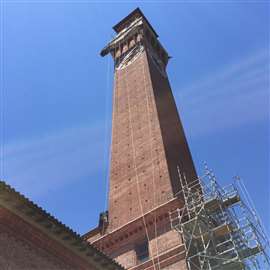
Suspended scaffolds are also affected by Mr. Euler’s research but perhaps not in way you might expect. Columns in tension are not influenced by the unbraced length and therefore wire ropes can support tremendous loads relative to their diameter. Where Euler’s three factors shine is in the horizontal cantilever beam to which the suspension rope is attached. While the load of the suspended scaffold does not apply an axial compressive load, it does apply a bending load at the outboard end of the cantilever beam. If the beam shape is incorrect, the material strength is inadequate, or there is insufficient bracing of the beam, the beam will roll, twist, bend, and ultimately be incapable of supporting the scaffold load, resulting in an unfavorable outcome for the scaffold occupants.
Today’s world
Design and analysis of scaffolding stems from research initiated by physicists three hundred years ago. It introduced certainty in the design of structures and scaffolding, and economized construction. Over time, it ended the practice of building structures that was based on a builder’s experience and past performance.
In today’s world, no significant structure is designed or built without utilizing the science we know today as engineering. Except for scaffolding.
Amazingly, the scaffold industry still constructs scaffolds the way it was done in 1700, relying on erectors who, absent the knowledge of the concept of the unbraced length, hope to get it right based solely on past experience. More amazing, it is considered an acceptable practice.
STAY CONNECTED



Receive the information you need when you need it through our world-leading magazines, newsletters and daily briefings.
CONNECT WITH THE TEAM



