Automatically translated by AI, read original
Intelligentere, sicherere und nachhaltigere Traggerüst- und Schalungslösungen
10 June 2024
Fortschritte wie BIM, Vorfertigungstechniken und die Integration von Automatisierung verbessern bereits die Effizienz, Sicherheit und Qualität von Bauprozessen. Wie werden diese in der Branche genutzt?
Durch den Material- und Technologiefortschritt sind Lehrgerüst- und Schalungssysteme effizienter, langlebiger und anpassungsfähiger geworden und werden den steigenden Anforderungen moderner Bauprojekte gerecht.
Robert Hauser, CEO von Doka, ist sich bewusst, dass Technologie der Schlüssel zur Zukunft ist und das Unternehmen treibt die Entwicklung innovativer Produkte und Dienstleistungen für Anwender in der Branche voran.
Laut Hauser ist Doka durch digitale Tools wie BIM (Building Information Modeling) in der Lage, 3D-Modelle für Schalungen zu erstellen, den Materialeinsatz zu optimieren und so eine perfekte Passform sicherzustellen.
Mit Concremote optimiert Doka zudem digitale Tools. Das Betonüberwachungssystem des Unternehmens misst über Sensoren die Temperatur und berechnet die Druckfestigkeit der Betonkonstruktion.
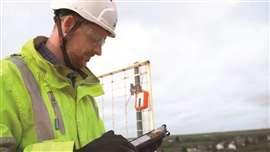
Betonsensoren
Auch das Bauunternehmen Costain verwendet Betonsensoren. Das Unternehmen nutzt die Betonsensoren von Maturix, um die Temperatur und Festigkeit von Beton bei Schalungsprojekten zu überwachen.
Die Technologie wurde in mehreren Costain-Projekten in den Bereichen Straße, Wasser und Schiene implementiert.
Die Gaia 200-Sensoren, die so groß wie ein Smartphone sind, senden Temperatur- und Festigkeitsdaten in Echtzeit drahtlos an Ingenieure, Planer temporärer Bauvorhaben und andere Fachunternehmer.
Costain sagt, dass die Informationen den Benutzern helfen können, schnellere und fundiertere Entscheidungen zu treffen. So können sie beispielsweise festlegen, wann die Schalung nach dem Betonieren entfernt werden soll.
Durchschnittlich soll sich durch die Einführung dieser Sensoren die Verweildauer der Schalung um etwa 33 % verkürzt haben.
Bei einem Costain-Projekt wurden die Sensoren bereits für über 80 verschiedene Gussteile und Strukturen eingesetzt, wodurch die Notwendigkeit einer zerstörenden Prüfung von etwa 500 Schlagwürfeln entfiel.
Bhavika Ramrakhyani, Materialleiterin bei Costain, kommentierte: „Wir spielen eine wichtige Rolle bei der Maximierung der Effizienz für unsere Kunden, ohne Kompromisse bei Qualität oder Sicherheit einzugehen. Es ist wichtig, dass unsere Ingenieure zum richtigen Zeitpunkt sofortigen Zugriff auf die richtigen Informationen haben und wichtige Informationen direkt an ihre Geräte und Laptops gesendet werden.
„Auf diese Weise können sie fundierte Entscheidungen treffen und genau bestimmen, wann es am sichersten ist, das temporäre Lehrgerüst und die Schalung nach dem Betonieren zu entfernen.“
Ramrakhyani fügt hinzu: „Wir haben bereits enorme Effizienzgewinne festgestellt. Die Geschwindigkeit der Programmbereitstellung hat sich erheblich verbessert, und die Zündzeiten haben sich an Standorten, an denen wir die Sensoren eingesetzt haben, um ein Drittel verkürzt.
„Gleichzeitig ermöglicht uns die Technologie, mehr unserer temporären Strukturen umzufunktionieren und wiederzuverwenden. Außerdem können wir die Menge der verwendeten Materialien reduzieren und so unseren CO2-Fußabdruck verringern, was ein weiterer großer Vorteil ist.“
Innovationspotenzial
Wie Costain ist sich Hauser bewusst, dass ein enormes Innovationspotenzial besteht, das die Herstellung und Verwendung von Schalungen auf Baustellen revolutionieren könnte.
Er fügt hinzu, dass Fortschritte wie BIM, Vorfertigungstechniken und die Integration von Automatisierung bereits heute die Effizienz, Sicherheit und Qualität von Bauprozessen verbessern und dass wir davon in Zukunft noch mehr sehen werden.
Das Robotikunternehmen Saeki versucht, neue Technologien in die Schalungsindustrie einzuführen. Die Roboter des Unternehmens stellen 3D-gedruckte Schalungen her, mit denen nicht standardmäßige und kundenspezifische Bauelemente risikofrei hergestellt werden können.
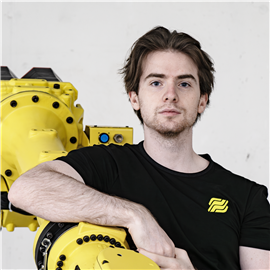
Laut Saeki stellt dies eine kostengünstige, nachhaltige Lösung für die Kleinserienproduktion nicht standardmäßiger Betonelemente dar.
Das Startup arbeitet derzeit mit nur zwei Robotern, die unabhängig voneinander Schalungen herstellen. Diese Schalungen werden direkt an Bauunternehmen geliefert, die sie auf Baustellen einsetzen, oder an Hersteller, die die Betonelemente vorfertigen und an Bauunternehmer verkaufen.
Das ultimative Ziel des Unternehmens besteht jedoch nicht darin, als Hersteller von 3D-gedruckten Schalungen aufzutreten, sondern vielmehr darin, Abonnements für seine Dienste für den 3D-Druck von Schalungen und anderen Komponenten zu verkaufen.
Im Rahmen dieses Geschäftsmodells, das als „Robotik als Dienstleistung“ bekannt ist, plant Saeki die Entwicklung mehrerer 3D-Druckzentren, die jeweils aus mindestens 10 Robotern bestehen. Auf diese Weise können Kunden aus aller Welt Zeit mit den Robotern buchen, um regelmäßige Bestellungen abzuwickeln.
Andrea Perissinotto, einer der Mitbegründer des Unternehmens, sprach mit Construction Briefing. Er sagt, wenn 3D-gedruckte Schalungen in großem Maßstab eingesetzt werden, hat dies das Potenzial, den Bau- und Designprozess grundlegend zu verändern und die Menge des verwendeten Betons zu reduzieren.
„Bis zu 80 % der in einem modernen Gebäude verwendeten Materialien müssen dort nicht vorhanden sein“, sagt Perissinotto.
„Es ist nicht nötig, 30 Zentimeter Beton durch ein ganzes Gebäude zu gießen. Es ist einfach billig, das zu tun, weil Beton billig ist. Indem man die Geometrie eines Gebäudes und die Lasten, die darauf einwirken, optimiert, kann man viel Beton aus dem Gebäude herausnehmen.
„Derzeit sind diese Verbindungsdetails sehr teuer, denn wenn Sie eine optimierte Säule erstellen, weist sie einige komplizierte Details auf und es ist einfach billiger, eine dickere Platte zu gießen. Mit 3D-gedruckten Schalungen sind diese geometrischen Einschränkungen jedoch keine Einschränkungen mehr.“
Nachhaltige Entwicklungen
Auch bei den jüngsten Innovationen der Branche steht die Nachhaltigkeit im Mittelpunkt. Ein Beispiel hierfür ist die Entwicklung leichter, wiederverwendbarer Schalungssysteme, die Abfall und Umweltbelastung minimieren.
Für Hauser von Doka liegt die Zukunft des Gerüst- und Schalungsbaus in intelligenteren, sichereren und nachhaltigeren Lösungen.
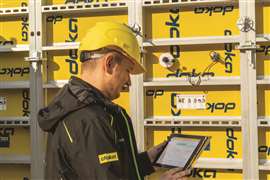
Nachhaltige Lösungen stehen für Doka im Mittelpunkt, da das Unternehmen nach Möglichkeiten sucht, Emissionen zu reduzieren. Hauser betont, dass das in Österreich ansässige Unternehmen datengesteuerte Nachhaltigkeit nutzt, um die Treibhausgasemissionen (THG), die von seinen Produkten in den jeweiligen Phasen des Materiallebenszyklus erzeugt werden, zu messen.
Auf diese Weise können Benutzer ihre Umweltauswirkungen besser verstehen und Möglichkeiten zur Reduzierung ihrer Emissionen durch die Auswahl umweltfreundlicherer Produkte und Systeme in Betracht ziehen.
Für Hauser und Doka besteht das ultimative Ziel darin, von Natur aus nachhaltige Produkte zu schaffen, die für die Verwirklichung der Netto-Null-Emissionsstrategie des Unternehmens bis 2040 von entscheidender Bedeutung sind.
Er fügt hinzu: „Modernste Materialien tragen nicht nur dazu bei, Produkte umweltfreundlicher zu machen, sondern verbessern durch die Verwendung leichterer Materialien und verbesserter Sicherheitsfunktionen auch die Handhabung.“
Derzeit gibt es viele bemerkenswerte und spannende Trends im Bereich nachhaltiges Bauen, doch ein Trend, der für Doka besonders hervorsticht, ist die Reduzierung der Umweltauswirkungen von Beton, insbesondere der erheblichen CO2-Emissionen.
Hauser sagt: „Seine Festigkeit, Haltbarkeit, Verfügbarkeit und andere Eigenschaften machen ihn für viele Jahre zu einem unverzichtbaren Baustoff in der Bauindustrie. Die Suche nach neuen Wegen, um das Bauen mit Beton nachhaltiger zu machen, erfordert die ernsthafte Aufmerksamkeit aller Akteure unserer Branche.“
Kohlenstoffarmer Beton
Eine vielversprechende Option, sagt Hauser, sei die Verwendung kohlenstoffarmer Betonmischungen, die weniger Klinker enthalten, aber insbesondere in kälteren Klimazonen längere Aushärtezeiten aufweisen.
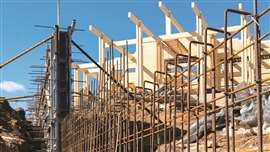
„Diese verlängerte Aushärtezeit bringt in der Praxis Kosten- und Effizienzprobleme mit sich, da sie sich auf die Projektzeitpläne auswirkt und erfordert, dass die Schalung über längere Zeiträume an Ort und Stelle bleibt.
„Jüngste gemeinsame Forschungsprojekte mit Branchenführern wie Strabag und Holcim in Österreich zielen darauf ab, Lösungen zu entwickeln, die die Leistungsstandards von kohlenstoffarmem Beton aufrechterhalten.“
Dokas Beitrag zu Projekten wie diesen umfasst die Entwicklung eines intelligenten Heizschalung-Prototypen, der die frühe Festigkeitsentwicklung beschleunigen und die praktische Umsetzung von CO2-reduziertem Beton erleichtern soll.
„Dazu gehören die Verwendung nachhaltigerer Materialien, Abfallreduzierung, Kreislaufwirtschaft und die Minimierung des CO2-Fußabdrucks von Bauprojekten“, sagt Hauser.
„Viele der Lösungen, die wir brauchen, um Netto-Null zu erreichen, gibt es bereits, aber andere müssen erforscht und weiterentwickelt werden. Hier liegt das größte Potenzial: im Verständnis von Nachhaltigkeit als Katalysator für die Entwicklung neuer Geschäftsmodelle, Produkte oder Dienstleistungen.“
Hauser ist sich einig, dass die Branche die Möglichkeit hat, mit gutem Beispiel voranzugehen und umweltfreundliche Praktiken für die Zukunft von Traggerüsten und Schalungen einzuführen.
STAY CONNECTED



Receive the information you need when you need it through our world-leading magazines, newsletters and daily briefings.
CONNECT WITH THE TEAM


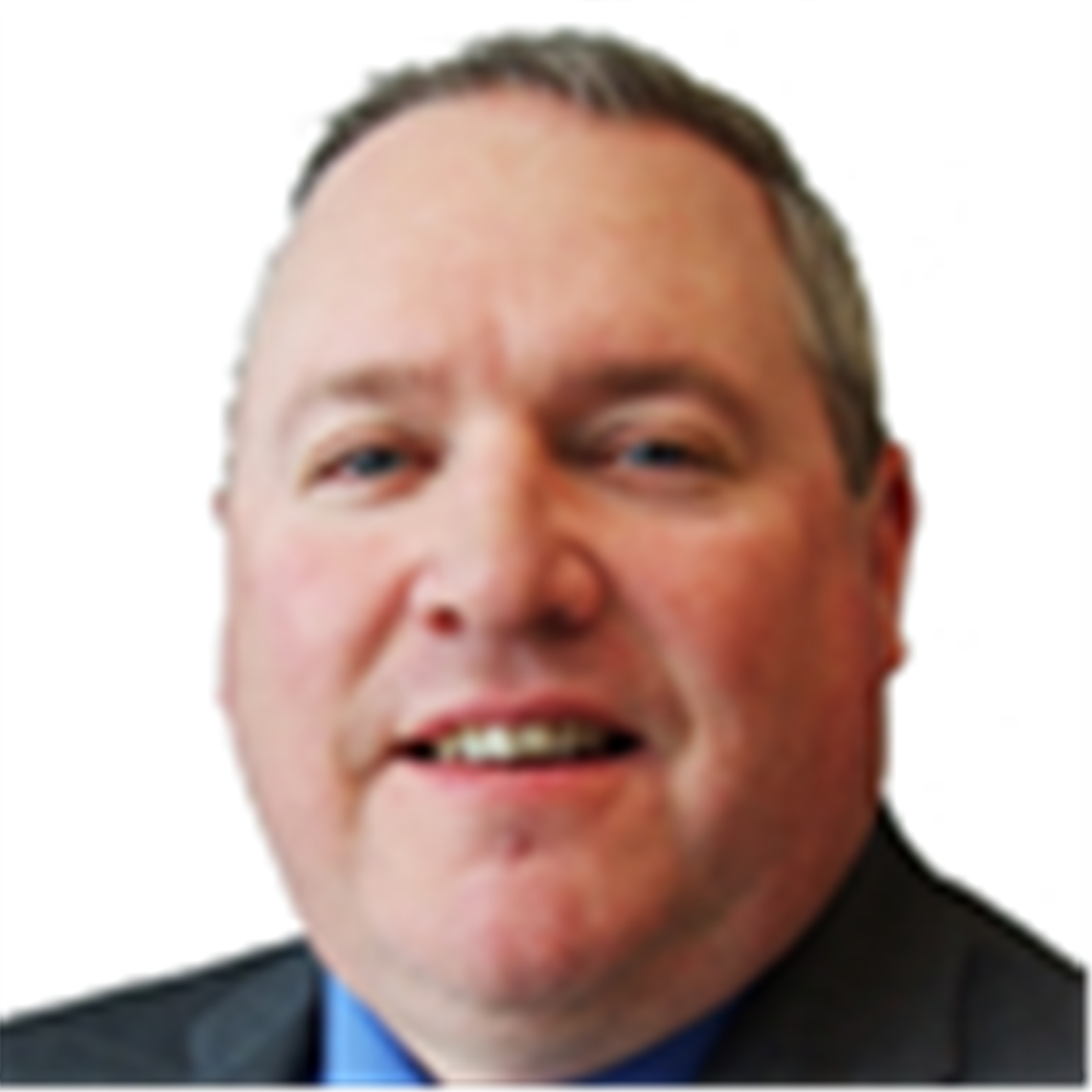
