Medical necessity from BrandSafway
June 28, 2023
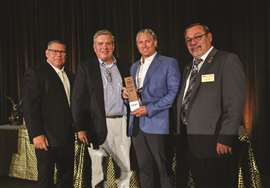
There’s an organized chaos about building demolition. “A lot of engineering and careful planning went into our scaffold solution for demolishing Queeny Tower in St. Louis,” explained Central Engineering Manager Ryan January. “We had to use extra precaution because of the tower’s close proximity to the Barnes Jewish Hospital, just next door.”
Demolition of the 227-foot-tall tower was required to make room for the construction of a new inpatient center on the Barnes Jewish medical campus, the preeminent healthcare facility in St. Louis.
“The demolition was planned and executed on a floor-by-floor basis and performed by crews using excavators, skid loaders and other smaller equipment, which could be lifted by a crane and supported by each successive floor slab,” said January. “Using a wrecking ball or an implosion technique, which would generate an extreme amount of dust, wasn’t feasible due to the adjacent occupied hospital.”
In addition, noise, vibration, odors and dust were monitored continuously by a third-party contractor. Further, concerns about an ingress of airborne contaminants were especially high, as the demolition occurred during the Covid-19 pandemic.
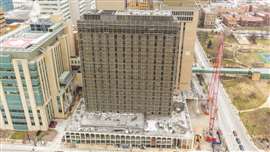
Standard debris netting (or scrim, which is the black synthetic fabric ubiquitous on construction sites) would not sufficiently contain the dust/debris and prevent it from infiltrating the adjacent hospital’s HVAC intake system. As a result, three sides of the building required a 95,567-square-foot plywood barrier in addition to scrim.
“As Ahrens (Ahrens Contracting, Inc., the general contractor) demolished one floor – or a portion of a floor – the scaffold debris shield would extend vertically to provide containment,” explained January. “After the demolition of a floor was completed, the cantilevered section would be dismantled.”
Withstanding high winds
Because the shield would exist unsupported for a period of time before dismantling, the cantilevered section needed to

withstand wind forces in excess of 90+ mph. And as anyone who has ever tried to manage an umbrella in a thunderstorm knows, high winds on a large surface area require greater strength to manage.
To be certain that the BrandSafway solution could withstand wind forces, BrandSafway used STAAD Pro, a Structural Analysis and Designing Program developed by Research Engineers International (REL). “STAAD Pro software is widely used by civil engineers for structural analysis and supports all types of various steel, concrete, and timber design codes,” explained January. “The program allows us to design any type of structure and share the synchronized model data with the entire design team.”
The next part of the demolition solution involved engineering a unique custom (and stronger) tie solution using Quick Erect Scaffold (QES) components to tie the building to the Systems Scaffold. Finally, to withstand high wind loads and provide good stiffness (torque), BrandSafway engineers designed the scaffold with extra tubes (cross braces), which clamped in both a horizontal and vertical X-pattern.
Prior to the Queeny Tower project, previous façade scaffold with plywood designs only allowed for a cantilevered section of approximately six feet, because plywood extensions could not withstand wind loads exceeding 90 mph. After 6 feet of demolition, contractors would need to stop; scaffold teams would need to come in, dismantle the scaffold and remove the building ties and plywood. BrandSafway worked with the customer to demonstrate how the solution would work in advance.
Enabling productivity
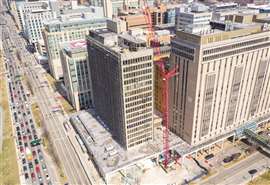
With the cross-bracing and building ties, the BrandSafway façade design allowed the Systems Scaffold to cantilever a maximum distance of 11 feet, 6 inches past the last tie. By essentially doubling the maximum height between ties, BrandSafway reduced the number of times, from 38 to 20, that the scaffold crew needed to dismantle scaffold as demolition proceeded. Here’s the math: With the 227-foot-tall tower, if just six feet per cantilever section were removed each time, the crew would need to dismantle 38 times. But by removing 11 and a half feet each time, the BrandSafway crew was required for dismantle just 20 times – almost a 50 percent reduction in dismantle operations.
The Queeny Tower demolition project earned BrandSafway the winner of the 2022 Scaffold & Access Industry Association Project Award in the Supported Scaffold Project of the Year category.
The Supported Scaffold Project award is presented to a member company where supported scaffolding was utilized to: raise the overall level of safety on a project, contribute to the overall success of the project, or complete a dynamic installation in a new or innovative way.
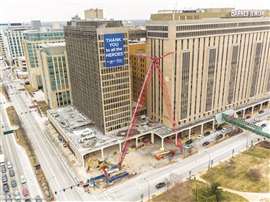
Queeny Tower facts
Edgar Monsanto Queeny and his wife, Ethel, donated $4.5 million for the construction of Queeny Tower, half the total cost.
The tower stood at 321 feet tall. Queeny Tower opened in 1965.
The building featured a mix of hospital beds, doctors’ offices, hotel rooms, parking, a restaurant and an 18th floor swimming pool.
The Queeny Tower Hotel closed in 1997. The 17th floor restaurant closed Nov. 14, 2016. In 2019, the building was vacated, closing in November.
BrandSafway fact
BrandSafway reduced the number of times that the scaffold crew needed to dismantle scaffold as demolition proceeded by almost 50 percent.
STAY CONNECTED



Receive the information you need when you need it through our world-leading magazines, newsletters and daily briefings.
CONNECT WITH THE TEAM



