New tech, lifting capacity and sustainability: the growth of SPMT trailers
November 25, 2021
Increasing lifting capacity of SPMT trailers means bigger loads are on site and on the road. Niamh Marriott reports.
Ludo Mous, operations director, global SPMT fleet at Mammoet, says, “We see a general increase in the lifting capacity of SPMT trailers up to 60 tonnes per axle line, and stronger frames. While this is an impressive engineering development, during any given lift the capacity of the SPMT trailers is not the only enabling or limiting factor. It is not always possible to utilise the full 60 tonne capacity per axle line, because, for example, the automatic increase in pressure exerted by the tyres sometimes cannot be borne by the underlying ground. In our experience, there are only limited projects during which the full 60 tonne capacity can be used safely.”
The limit seems to depend upon the strength of the road to take the weight, rather than any limit with the technology itself.
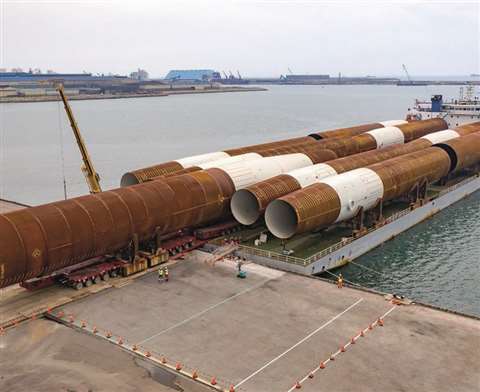
“Where in the past we only had four and six-line transporters, now we see a need for five-line SPMTs more and more. Over the years, split trailers have been added to our fleet. This is due to smaller allowable axle line loads on public roads,” he continued. “Thorough route surveys are required to assess the strength of the ground (among many other factors) before the correct SPMT transport strategy can be decided upon. Depending on the bearing capacity of the ground, SPMT transport solutions may require significant prior engineering work.”
“The ultra-high capacity SPMT models, of 40 to 60 tonnes per axle lines, can only be used where the ground below them is strong enough to carry these increased loads – this is the limiting factor, rather than how much weight the SPMT itself can carry.”
Mammoet and SPMT trailers
Mammoet has added onboard electrical systems to its SPMT trailers. “This has allowed us an opportunity to monitor our fleet more closely to identify long-term trends in their usage, and to simplify configuration of the trailers themselves,” said Mous. “SPMTs are highly complex pieces of equipment – each set of wheels has its own independent hydraulics system that must be set up in the right way to ensure the stability of the load.”
Lifting and moving heavy loads is a risky business and needs detailed preparations. Electrical tests can aid in this prep. Hareket’s new load cells preceisely weigh loads and check all calculations to minimise risk. The cells can weigh single loads up to 8,400 tonnes with 14 units as each load cell has 600 tonne weighing capacity.
Sustainable SPMT technology
Being sustainable is certainly coming to the forefront of SPMT technology as well as with transportation in general. “We are always looking for ways to operate more sustainably, and our SPMT fleet is no exception,” said Mous. Alongside SMPT manufacturer Scheuerle, owned by heavy duty and special vehicle manufacturer Transporter Industry International Group (TTI Group), Mammoet is working on getting its electric PPU ready for active service.
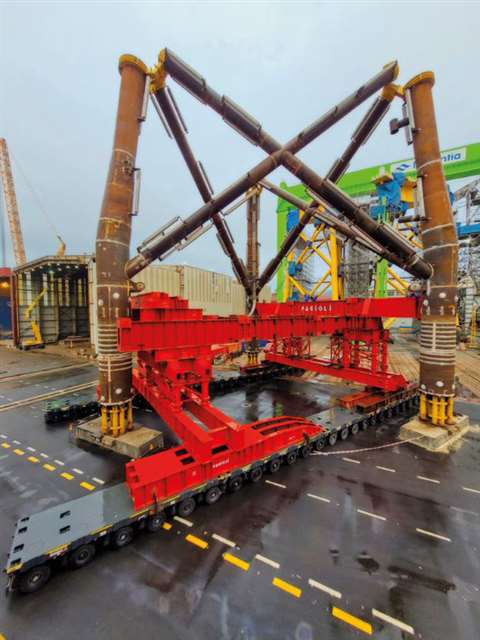
“More recently we completed our first SPMT project using HVO fuel – a site transport of two topsides, weighing a combined 2,000 tonnes,” said Mous.
Wind farm construction
SPMTs are continually being used for wind farm construction, both onshore and offshore.
“The wind industry places heavy demand on our equipment; specifically, for marshaling activity of nacelles, tower sections and foundations for offshore wind projects,” said Ludo Mous. “SPMTs will be used for the load-out of larger floating wind foundations, for example during the WindFloat Atlantic project a few years ago. The onshore marshaling of all of these components also keeps our SPMTs occupied.”
These wind farm projects demand high capacity SPMTs. Cometto, part of the Faymonville Group, worked with Fagioli on a contract for Navantia, to transport and load out several jackets in Northern Spain, for a new offshore wind farm. The weight of the items were massive - 480 tonnes for the carpentry of the transport structure, 600 tonnes for the lower and upper parts of the jacket and 1,200 tonnes for the complete jacket.
A tailor-made structure had to be designed and assembled in order to move the lower and upper parts of the jackets, so that they could be joined together and prepared for the load out operation that will take place in early 2022. Cometto had to use 56 axle lunes of SPMT with a capacity of 48 tonnes per axle lines. The transporters were divided in an open compound with two convoy lanes of 28 axle lines, propelled by two 368 kilowatt power pack units. The total payload capacity of the configuration was 2,500 tonnes.
Engineering and planning was needed when Mammoet collaborated with Cometto to transport a tripod foundation, a bulky item which had a height of 90 meters and weighed 2,035 tonnes. The Mammoet crew transported the load on 84 axle lines Cometto MSPE with a payload capacity of 48 tonnes per axle line, and three power pack units with an output of 368 kilowatts each. The tripod foundation is part of an offshore wind project that is called Seagreen OWF, a joint venture between TotalEnergies and SSE Renewables. The windfarm, which will house 140 turbines, is located 27 kilometres off the coast of Angus in the North Sea.
Wind turbine blades also require specialist thinking when it comes to transportation. German heavy haulage company Goldhofer unveiled their latest FTV 850 blade transporter, its biggest ever blade lifter. It can be used in the standard 3 metre width but also with split combinations in widths of up to 4 metres. The first FTV 850s are already on their way to Anipsotiki and Denzai, and were recently used by Laso to transport blades to a wind farm in Spain. Laso used three blade lifters from Goldhofer, a FTV500, a FTV550 and the new FTV850.
Mammoet oil and gas
Mammoet also see SPMT need in oil and gas projects.
“Our larger oil and gas projects make heavy use of SPMT transporters, for example when we loaded our the Aibel main support frame module in Thailand recently,” said Mous. “Our larger LNG projects, for example LNG Canada, also require many SPMT transporters to be mobilised.”
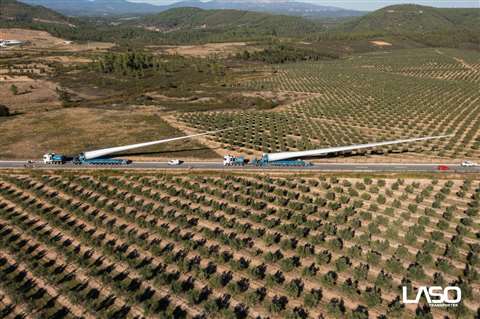
In Oman, Hareket was chosen as heavy lift contractor for offsite and utilities packages by Petrofac and Samsung JV in Duqm Refineries. The refinery is a strategic investment for the Sultanate of Oman and is part of Oman’s special economic industrial zone. Hareket will engineer, supervise and perform some critical heavy lifting works, including tandem lifts of up to 1,600 tonnes and an installation of 190 metre high flare.
Elsewhere in Oman, Fagioli was contracted by L&T Modular Fabrication Yard LLC to transport and load out a D30-2 jacket at their modular fabrication yard in Sohar, Oman. The jacket, weighing 3207te and was 92 metres long, 37.7 metres wide and 37.4 metres high, was transported by SPMT. Fagioli used 144 axles and 7 power pack units. Whilst a 300 class barge was supplied by the client, management of barge including mooring and ballasting was under Fagioli’s scope, and the project was engineered and executed safely and successfully.
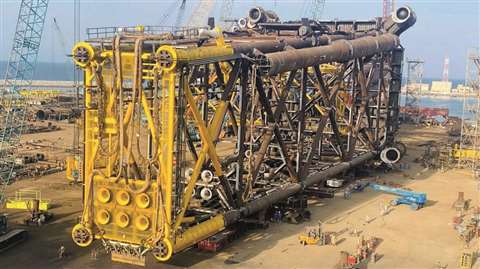
SPMT transportation
“Engineering needed to perform SPMT transportations is significantly underestimated in industry,” said Mous. “As maximum axle line loads are now increasing, margins are getting smaller. This has consequences, if all engineering isn’t performed to a high standard. Mammoet is one of the few companies using dynamic factors in its calculations, using its in house program, EZTrailer, that was developed in combination with DNV.”
“Even after 40 years of operating SPMT trailers and engineering successful lifts using them, we are still receiving new input. For example, we have performed tests to analyse the braking forces of an SPMT trailer, or the stability of loads approaching their tipping point, which have given us some unexpected results that have increased safety in the field. This is the value of thorough engineering.”
STAY CONNECTED



Receive the information you need when you need it through our world-leading magazines, newsletters and daily briefings.
CONNECT WITH THE TEAM



