PPS Awards honor innovation in technologies - Part 1
13 November 2024
The Power Progress Summit Awards recognize the products and people behind the innovations driving the industry forward. In this first of two parts, we look at the products securing the win for 2024.
In recent years, we’ve seen an array of innovative technologies emerge intended to reduce or eliminate emissions, enhance fuel efficiency and/or improve performance and safety on work sites. Those technologies form the core of the annual Power Progress Summit Awards program.
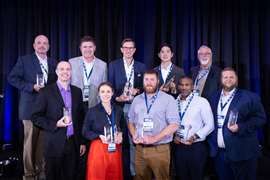
This year, we not only recognized select new technologies and the companies that launched them – we also honored those behind the scenes who worked to develop them and to support them once they left the factory floor.
In Part 1 of this two-part feature, we provide an overview of the 2024 new product award winners as selected by our distinguished independent panel of judges. Part 2 will highlight the winners in the Off-Highway Product Application of the Year, Engine Distributor of the Year and Product Development Team of the Year categories.
To learn more about the awards as well as the judging panel, visit PowerProgressSummit.com.
Achievement of the Year
First recognized in the Control System/Monitoring Solution of the Year category, John Deere’s Attachment Manager Technology proved a standout with the judges in selecting the recipient of the top award from among the category winners.
Available as an upgrade on the 330, 331 and 333 P-Tier machines and standard on the 334 and 335 P-Tier models, the Attachment Manager technology was developed to take the guesswork out of determining optimal attachment performance parameters by enabling preprogrammed flow and pressure for John Deere attachments.

Included with the software is a list of pre-loaded attachment settings that are recommended for optimal performance when using Deere-designed attachments. Once an attachment is selected, the machine will automatically set up with those parameters.
During operation, attachment selection can be done through the in-cab display. The three most critical performance features are then displayed on the monitor, as well as the hydraulic pressure gauge and an image of the attachment for quick identification.
Newly designed joystick controllers come pre-programmed with attachment-specific control papers. Operators do not need to remove their hands from the joystick to enable or disable functions or use other buttons or switches to properly control the attachment. Instead, it can all be achieved directly on the joysticks.
The Attachment Manager enables operators to save attachment settings and load new settings as needed, with up to 20 specific attachments appearing on the display. In addition, the system provides constraints to certain machine settings that prevent things such as higher pressure or higher flows from being selected that may cause issues with Deere attachments.
The judging panel was impressed with this “smart attachment” technology, calling it a huge step forward.
“As you know, the next generations aren’t growing up with the same experiences as prior generations [of operators],” one of the judges noted. “Having things [like] a smart attachment is not only going to make it easier for the operator, but it’s also going to make it safer.
“It hopefully brings another level of safety to the people who are not in the in the cab of the machine,” he added.
Engine of the Year
In what proved to be the most competitive year of judging for this category to date, the judges struggled to narrow down the choices to a single winner. Ultimately, one selection floated to the top: Caterpillar’s C13D diesel engine.

The 13-liter C13D inline six-cylinder diesel engine is designed for optimal power density, torque and fuel efficiency in heavy-duty off-highway applications. It will offer eight power ratings from 456 to 690 hp (340 to 515 kW) with up to 3,200 Nm of peak torque. This is a 20% increase in power and up to 25% more low-speed torque over previous Cat engines in this power class.
The C13D will meet the emissions standards of higher regulated territories, such as EU Stage V and U.S. EPA Tier 4 Final, with models available for lesser regulated countries. By modularizing and eliminating components, its architecture is space-protected to accommodate configuration adjustments anticipated for future tiers of emission standards in the U.S. and EU without relocating customer connection points, Caterpillar noted. In addition, its core architecture is designed for future development of natural gas and hydrogen fuel capabilities.
By supplying comparable power and torque available from its current 13 L, 15 L and single-turbo 18 L platforms, the C13D platform enables OEMs to downsize the engine while simplifying design and assembly, Caterpillar asserted.
Engineers plan to make early OEM pilots available in 2025, with the production of industrial variants scheduled to begin in 2026.
In selecting the C13D for Engine of the Year, the judges appreciated that its simplified design took assembly into account. They also pointed to its high-power density and torque and the emphasis on sustainability, such as its compatibility with biodiesel fuels.
Engine Technology of the Year
There was little hesitation when it came to selecting the winner in this category: Cummins Valvetrain Technologies’ valvetrain for the X15 HELM engine platform.

The new valvetrain was described as “one of the most advanced valvetrain systems that Cummins has produced.” It was developed by the Cummins Valvetrain Technologies (CVT) team, which was formed following the acquisition of Jacobs Vehicle Systems in 2022.
A fundamental principle of the Cummins HELM platform is that the base engine has commonality across various fuel types, the award entry noted. It added that “developing a valvetrain for any customer takes considerable effort but developing a future-proofed valvetrain with multiple technologies to be used across varying markets, emissions regulations and fuel types takes it to the next level.”
The valvetrain is modularly designed to create a flexible engine platform as emissions tighten and customization is needed. It has a compression release Jake Brake that can be upgraded to Jacobs High Power Density (HPD) 2-Stroke Braking for increased braking performance when needed. The system also includes protection for Cylinder Deactivation as well as technologies such as HLAs and Variable Valve Actuation to be deployed on X15 engine variants that use alternative fuels such as natural gas and hydrogen.
A Double Overhead Cam Configuration provides a better arrangement of ports and valves for more efficient breathing of the engine.
In commenting on the new valvetrain’s selection as the category winner, one judge cited “the simplicity for manufacturing – to be able to adjust to whatever the customer’s needs are, which also sets him up for the future as alternative fuels continue to develop.” Another added: “They have a design strategy that allows them to be extremely flexible and change to the market demands.”
Powertrain Product of the Year
In developing the eSP502+PTO e-transmission, Dana’s cross-functional teams worked to design a sustainable, fully electric driveline system. The result was a flexible platform designed to support electrification of construction and material handling applications that utilize additional hydraulic work functions – all in one system.
The eSP502+PTO e-transmission combines a dual motor, two-speed powershift transmission for drive functions with independent controllable power take-off (PTO). The system delivers 200-kW continuous driveline power, with up to 250 kW in peak capability, and features the possibility to have a driveline connection on both sides to facilitate 4WD setup or increased vehicle integration flexibility.
The system is controlled by Dana’s driveline control unit, which offers a series of features to optimize driver experience while driving the application and controlling hydraulic functions connected to the PTO.
The addition of the PTO within the system is designed to provide flexibility for OEMs to reduce the installed electric power at vehicle level. Controlled utilization of Dana system electromotors manages the desired PTO power to drive work functions and the wheels independently in the majority of applications. In marginal cases where maximum tractive effort is required, the PTO can be disconnected, allowing full installed electrical power of both motors to be directed to the driveline.
Concept design of the PTO subsystem is ongoing and first prototypes are planned to be built in Q1 2025 and scheduled for validation through 2025, including vehicle integration at Dana test facility.
In selecting this entry, the judges especially appreciated that the system addresses separate functions, merging aspects of both drivability and powering work functions.
Electrification Technology of the Year
In selecting the Danfoss Editron ED3 onboard charger as the winner in this category, the judging panel noted that designing an AC 43-kW charger isn’t easy.

Typical electric vehicle (EV) onboard chargers provide 22 kW of power, as Danfoss pointed out in its award entry. For a heavy-duty vehicle or machine using an AC charger, charging time could range from 15 to 18 hours – too long for overnight charging. And while DC chargers can resolve this challenge, they come at a significantly higher cost.
With the launch of the ED3 onboard charger and electric power take-off (PTO), electric and hybrid machinery owners can maximize AC charging speeds and minimize charging infrastructure costs, Danfoss asserted, making electrification more attainable and reducing range anxiety.
The ED3 is a bidirectional onboard charger – which the judges appreciated – and an electric power supply designed to offer high charging power and distribute energy to a vehicle’s auxiliary functions. Designed for on-highway commercial trucks as well as off-highway machinery, the charger enables rapid overnight charging – another feature pointed to by the judges – as well as opportunity charging for vehicles using readily available utility outlets. The charger can deliver up to 43 kW to the main high-voltage battery and up to 44 kW of AC or DC power, as needed, to other subsystems.
The ED3’s AC and DC electric PTO pulls power directly from the main high-voltage battery to support up to 44 kW of DC power to auxiliaries, such as high-voltage compressors, pumps and motor controllers. The charger can also convert power and deliver up to 43.6 kVA of single- or three-phase AC current. This versatility gives OEMs flexibility in designing the vehicle’s system architecture, Danfoss stated, and enables standardization of components across platforms.
STAY CONNECTED



Receive the information you need when you need it through our world-leading magazines, newsletters and daily briefings.
CONNECT WITH THE TEAM


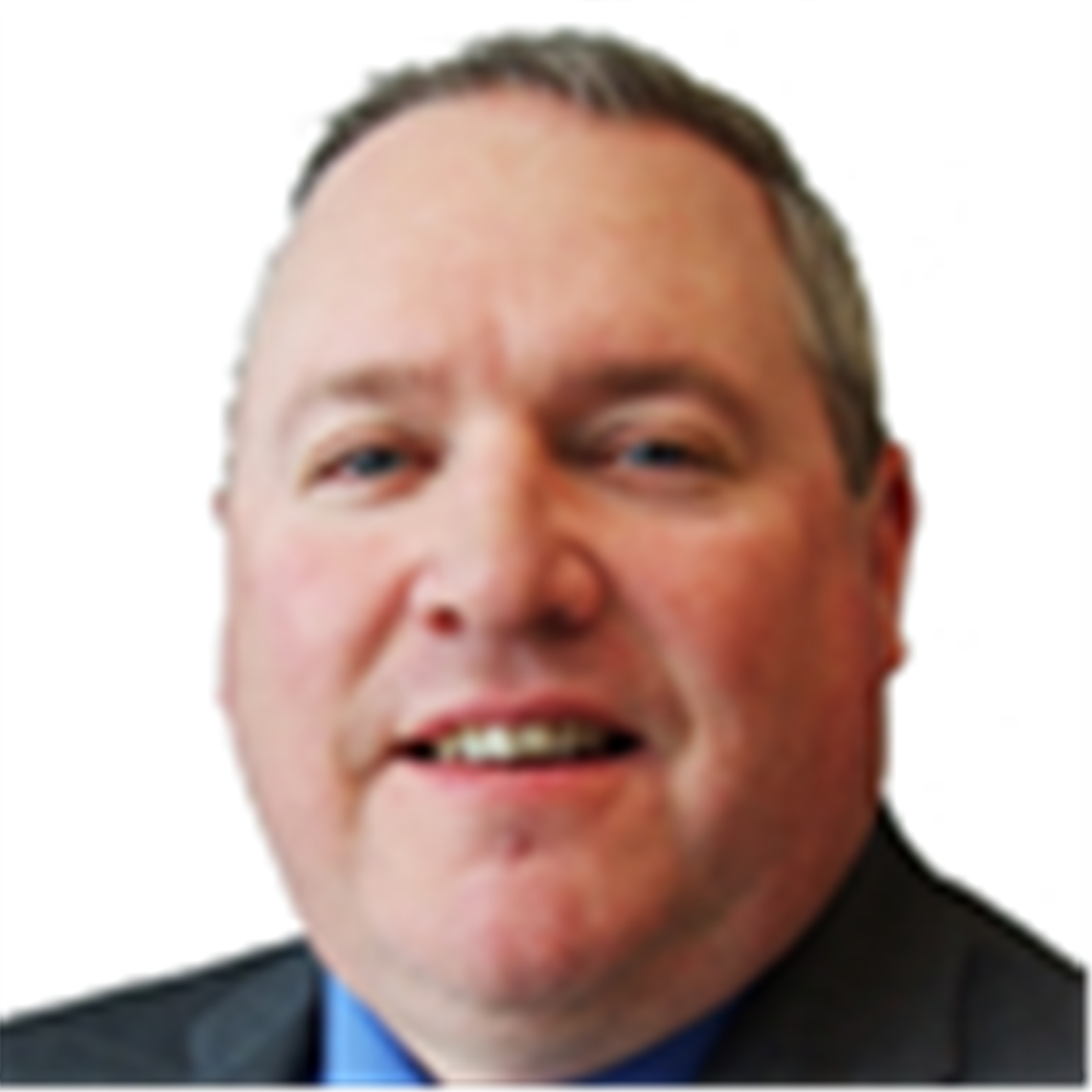
