Princess Elisabeth: cranes are crucial for island-building factory
26 September 2024
Princess Elisabeth Island is set to become the world’s first ‘energy island’ – a multi-billion Euro artificial island in the North Sea designed to gather the electricity produced by the growing number of wind turbines in the area and send it to shore in a more efficient manner. Lucy Barnard finds out how it is being built.
At the TM Edison fabrication yard in Vlissingen, Netherlands, workers are busy pouring concrete to make huge reinforced concrete blocks the size of a 10-storey apartment building. One day they will form the foundations for a huge new island.
Each massive cuboid is 57 metres long, 30 metres wide and 30 metres high, and weighs 22,000 tonnes. It takes a team of around 300 workers three months to build a single block.
Once ready, the blocks – or caissons – will be floated out to sea, towed by tugboat to a spot in the ocean about 45 kilometres off the coast of Ostend in Belgium. There they will be sunk and dredgers will fill them with sand to form the foundations of a project designed to turbocharge offshore wind power in the North Sea.
Watching their progress on a suitably windswept but sunny morning earlier this year, outgoing Belgian Prime Minister Alexander de Croo, said Princess Elisabeth Island, as the new structure will be known, will act as a sort of mega electricity sub-station connecting the growing number of wind farms being built in the North Sea, helping to radically reduce the use of fossil fuels across Europe and curbing the continent’s reliance on Russian gas.
“The North Sea is set to become the powerhouse of our energy independence, and Princess Elisabeth Island will be a crucial part of this process,” de Croo told reporters on an official visit to the yard. “Belgium has long been a pioneer in offshore wind and, by continuing to innovate, we are further consolidating our position for the future.”
Certainly, it is easy to see why the project has found favour with politicians.
What are the advantages of energy islands?
Rather than today’s system where each offshore wind farm sends the power it generates to the national grid through its own dedicated cable, the project, which is being built by Belgian utility Elia for a reported €3.566 billion (US$3.9 billion), aims to gather the electricity from several wind farms at once and then send it onshore through one large cable in a cheaper and more efficient manner. Energy islands could also feed power to multiple countries based on demand.
With European countries pledging to build dozens of new wind farms in the North Sea, multiplying its total capacity from around 30 gigawatts today to 120 gigawatts by 2030 and 300 gigawatts by 2050 – enough to power every home on the continent – the need for an improved electrical infrastructure to distribute that power is growing increasingly stronger.
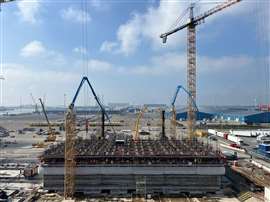
“Princess Elisabeth Island will be the world’s first artificial energy island that combines both direct current and alternating current,” said Jan Fordeyn, director of project development and conceptual design at Jan de Nul, one of the two Belgian dredging and construction companies awarded the engineering, procurement, construction and installation contract to build it.
“The island’s high voltage infrastructure will bundle the wind farm export cables of the Princess Elisabeth zone together, while also serving as a hub for future interconnectors with Great Britain and Denmark. The island will be the first building block of an integrated European offshore electricity grid.”
To reduce the risks and costs associated with building in such a remote spot, TM Edison is trying to ensure that as much of the complicated construction work takes place on land in its specially designed Vlissingen fabrication yard.
First concrete is poured to create the massive reinforced bases for the caissons before the cured base plates are moved on runners to a second station. There, a sliding formwork structure is set up and concrete is continuously poured into the huge moulds for around ten days, slowly rising to build the enormous walls at a rate of 100 millimetres every hour using electrically powered concrete pumps from German pump manufacturer Putzmeister.
Building blocks to make an island
“At peak times around 400 people per shift will be working on the construction site – making it approximately 800 people a day,” explains Fordeyn. “A variety of specialisations are required for the project. These include steel fixers for reinforcement, formwork and concrete labourers, crane operators, welders and electricians.”
After this, the partly-formed caissons are then slowly moved on runners to a third workstation where cable entries are added, followed by a further stop where a reinforced concrete roof is added and eventually storm walls.
The whole process takes around 85 days per caisson but, due to the workstation system, up to five caissons can be produced at the same time. In total about 165,000 cubic metres of concrete will be poured into the caissons.
“The biggest challenges for us are mainly related to the tight schedule of the project,” says Fordeyn. “Setting up a complete construction yard in less than six months has been one of the biggest challenges so far.”

To the cranes
At the time of writing six Liebherr tower cranes were at work in the construction yard, supplying rebar and other items to the upper slipform deck and towers for concrete pumps (four of which were rail-mounted to enable them to move about the site more easily). These include the 1,000 EC-H, the manufacturer’s largest standard tower crane, as well as a 550 EC-H, a 245 EC-H, three 340 EC-Bs and a single 280 EC-H.
Three telescopic crawler cranes; a Liebherr LTR 1100, a Sennebogen 653R-E, and a Marchetti CW70.42L, plus a Liebherr HS 8200 heavy duty lattice boom crawler crane were also in operation.
Most of the cranes were rented to TM Edison by their parent companies Jan de Nul and DEME, although a spokesperson for the joint venture said it also used smaller rental mobile cranes for some jobs. Cranes working on the site were fitted with collision avoidance systems from AMCS in France.
Assembling the infrastructure of the energy island requires lifting and manoeuvring large structural elements and equipment. Teams used spreader beams produced by UK manufacturer Modulift to evenly distribute the load, especially for formwork sections. “Spreader beams have been integral to the construction of the concrete sections, with one formwork section weighing around 17 tonnes and 10 metres in length,” explained Ruben Verschueren, site superintendent civil works at TM Edison. “We are using a one-over-one configuration, utilising a MOD 34 spreader beam at the top and a MOD 24 on the bottom.”
Moving the caissons
When the caissons are fully cured, they are loaded out on a fully submersible barge and towed to a launching pit and floated away to a separate storage quay. When the dredging teams at sea are ready, the caissons are towed out to their final resting place by tugboats, carefully positioned using pre-laid anchors and winches and fully ballasted with water. Later a second vessel fills the caissons with sand and covers them with large amounts of rock to protect them from erosion.
Another of the major challenges the team face is the method of construction. Few such structures have ever been built in the blustery North Sea.
“The use of caissons in a marine infrastructure design is not as common in the North Sea region as it is in the Mediterranean,” Fordeyn admitted. “This means all the parties involved from suppliers to certifying agencies are confronted with aspects that are new to them.”
Once all the caissons are in place, teams from TM Edison will use dredgers to fill the core of the island with sand and compact it using vibroflotation. Once the main structure of the island is complete, teams then install a small harbour and helipad for maintenance visits.
Construction teams in a consortium led by French contractor Eiffage (through its Belgian Eiffage Métal subsidiary Smulders) and Dutch specialist HSM Offshore Energy, are responsible for designing, manufacturing, installing and commissioning four alternating current electrical substations on the island – two of which will be 1,050-megawatt substations.
Installation work on the island is scheduled from May 2025 until the start of 2029.
There too teams have already been busy assembling the structures in off site fabrication yards to reduce the amount of time and the number of people required for final assembly in the remote North Sea spot.
“The majority of the current scope [of the work] is onshore in the Smulders production facility at Vlissingen and the HSM facility in Schiedam,” said Marguerite Richebé, media relations officer at Eiffage. “The modules will be outfitted to the maximum extent possible to limit the works on the island.”
Fordeyn said TM Edison and Elia were also doing everything they could to make the remote location more hospitable for the workers required offshore during the installation phase in 2025.
“Shifts typically last for 12 hours for offshore workers,” he said. “During their time off on board the installation vessels there is good catering and a gym, video games and a multi-media movie system for entertainment. Also internet is provided so that offshore colleagues can keep in touch with friends and family.”
More islands to come
TM Edison and its competitors predicted more energy island construction work in the area in the near future.
In 2021 the Danish parliament passed a law on the design and construction of a 3 gigawatt artificial energy island in the North Sea 80 kilometres west of Jutland which would be more than twice the size of Princess Elisabeth Island. Two years later, however, it postponed a tender to build it due to the anticipated costs of construction and is thought to be looking at cheaper options such as potentially building a platform on piles.
Another proposal for a 6 square kilometre energy island complex known as the North Sea Wind Power Hub, in the Dogger Bank shipping area between the territorial waters of the Netherlands, Germany and Denmark, is being worked up by Dutch grid operator TenneT, its German subsidiary and Danish power company Energinet.
“We believe it is a matter of time before other energy islands are built,” said Fordeyn. “The North Sea has favourable conditions for islands. It is relatively shallow and there is a lot of infrastructure to be accommodated.”
MAGAZINE
NEWSLETTER
The gold standard in market research
Off-Highway Research offers a library of more than 200 regularly updated reports, providing forensic detail on key aspects of the construction equipment industry.
Our detailed insights and expert analyses are used by over 500 of the world’s largest and most successful suppliers, manufacturers and distributers, to inform their strategic plans and deliver profitable growth.