Automatically translated by AI, read original
Soluciones de cimbra y encofrado más inteligentes, seguras y sostenibles
10 June 2024
Avances como el BIM, las técnicas de prefabricación y la integración de la automatización ya están mejorando la eficiencia, la seguridad y la calidad en los procesos de construcción. ¿Cómo se están utilizando en la industria?
Con los avances en materiales y tecnología, los sistemas de cimbra y encofrado se han vuelto más eficientes, duraderos y adaptables, satisfaciendo las demandas cambiantes de los proyectos de construcción modernos.
Robert Hauser, CEO de Doka, entiende que la tecnología es la clave para el futuro y la empresa está impulsando el desarrollo de productos y servicios innovadores para los usuarios de la industria.
Hauser explica que las herramientas digitales como BIM (Building Information Modelling) permiten a Doka crear modelos 3D para encofrados, optimizando el uso del material y garantizando así un ajuste perfecto.
Doka también optimiza las herramientas digitales con Concremote, un sistema de monitorización del hormigón que mide la temperatura y calcula la resistencia a la compresión de la estructura de hormigón mediante sensores.
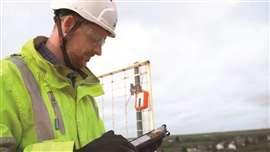
Sensores de hormigón
La empresa constructora Costain también utiliza sensores de hormigón. La empresa utiliza los sensores de hormigón de Maturix para controlar la temperatura y la resistencia del hormigón fraguado en proyectos de encofrado.
La tecnología se ha implementado en varios proyectos de Costain en los sectores de carreteras, agua y ferrocarriles.
Los sensores Gaia 200, que son tan grandes como un teléfono inteligente, envían datos de temperatura y resistencia en tiempo real de forma inalámbrica a ingenieros, diseñadores de obras temporales y otros contratistas especializados.
Costain afirma que la información puede ayudar a los usuarios a tomar decisiones más rápidas y mejor informadas. Por ejemplo, pueden decidir cuándo retirar el encofrado después de verter el hormigón.
En promedio, se dice que la introducción de estos sensores ha reducido el tiempo que el encofrado permanece en su lugar en aproximadamente un 33%.
Un proyecto de Costain ya ha utilizado los sensores para más de 80 vertidos y estructuras diferentes, eliminando la necesidad de realizar pruebas destructivas de aproximadamente 500 cubos de impacto.
Bhavika Ramrakhyani, responsable de materiales de Costain, comentó: "Tenemos un papel importante que desempeñar a la hora de maximizar la eficiencia para nuestros clientes sin comprometer la calidad ni la seguridad. Es importante que nuestros ingenieros tengan acceso instantáneo a la información correcta en el momento adecuado, con información crucial enviada directamente a sus dispositivos y computadoras portátiles.
“Esto significa que pueden tomar decisiones informadas para determinar con precisión cuándo es más seguro retirar el encofrado y la cimbra temporales después de un vertido”.
Ramrakhyani añade: "Ya hemos visto enormes beneficios en términos de eficiencia. La velocidad de ejecución del programa ha mejorado considerablemente y los tiempos de ejecución se han reducido en un tercio en los sitios donde hemos utilizado los sensores.
“Al mismo tiempo, la tecnología nos permite reutilizar más de nuestras estructuras temporales, así como reducir la cantidad de materiales utilizados, disminuyendo así nuestra huella de carbono, lo que constituye otro beneficio importante”.
Potencial de innovación
Al igual que Costain, Hauser reconoce que existe un inmenso potencial de innovación para revolucionar la forma en que se fabrican y utilizan los encofrados en las obras de construcción.
Añade que avances como BIM, técnicas de prefabricación y la integración de la automatización ya mejoran la eficiencia, la seguridad y la calidad en los procesos de construcción y que veremos más de esto en el futuro.
La empresa de robótica Saeki está intentando introducir nuevas tecnologías en el sector del encofrado. Los robots de la empresa fabrican encofrados impresos en 3D para fabricar elementos de construcción no estándar y personalizados sin riesgo.
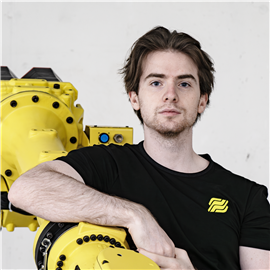
Saeki afirma que esto proporciona una solución rentable y sostenible para la producción de bajo volumen de elementos de hormigón no estándar.
Actualmente, la startup opera con tan solo dos robots que trabajan de forma independiente para crear encofrados. Estos encofrados se envían directamente a las empresas constructoras para su uso en las obras o a los fabricantes que prefabrican los elementos de hormigón y los venden a los contratistas.
Sin embargo, el objetivo final de la empresa no es actuar como fabricante de encofrados impresos en 3D, sino más bien vender suscripciones a sus servicios de impresión 3D de encofrados y otros componentes.
En el marco de este modelo de negocio, conocido como “robótica como servicio”, Saeki prevé desarrollar varios centros de impresión 3D, cada uno de ellos compuesto por al menos 10 robots. Esto permitirá a los clientes de todo el mundo reservar tiempo con los robots para cumplir con los pedidos habituales.
Andrea Perissinotto, uno de los cofundadores de la empresa, habló con Construction Briefing y afirmó que, si se adopta el encofrado impreso en 3D a gran escala, tiene el potencial de cambiar radicalmente el proceso de construcción y diseño y reducir la cantidad de hormigón utilizado.
“Hasta el 80% de los materiales que se utilizan en un edificio moderno no necesitan estar ahí”, dice Perissinotto.
"No es necesario verter 30 centímetros de hormigón en todo el edificio, simplemente es barato hacerlo porque el hormigón es barato. Al optimizar la geometría de un edificio y las cargas que se aplican sobre él, se puede sacar mucho hormigón del edificio.
“En la actualidad, estos detalles de conexión son muy costosos porque, si creas una columna optimizada, tendrá algún tipo de detalles intrincados y es más económico fabricar una losa más gruesa. Pero con el encofrado impreso en 3D, estas limitaciones geométricas ya no son limitaciones”.
Desarrollos sostenibles
La sostenibilidad también es un foco clave de las últimas innovaciones de la industria, ejemplificada por el desarrollo de sistemas de encofrado livianos y reutilizables que minimizan los desechos y el impacto ambiental.
Para Hauser de Doka, el futuro de los andamios y encofrados pasa por soluciones más inteligentes, seguras y sostenibles.
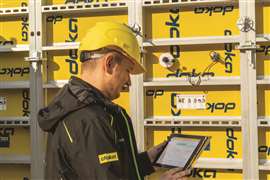
Las soluciones sostenibles están cobrando protagonismo para Doka, ya que la empresa busca formas de reducir las emisiones. Hauser destaca que la empresa con sede en Austria está utilizando la sostenibilidad basada en datos para medir las emisiones de gases de efecto invernadero (GEI) generadas por sus productos a lo largo de las fases relevantes del ciclo de vida del material.
De esta manera, los usuarios pueden comprender mejor su impacto ambiental y considerar las opciones para reducir sus emisiones seleccionando productos y sistemas más respetuosos con el medio ambiente.
Para Hauser y Doka, el objetivo final es crear productos inherentemente sostenibles que sean clave para lograr la estrategia de emisiones netas cero de la empresa para 2040.
Y añade: “Los materiales avanzados no sólo ayudan a que los productos sean más respetuosos con el medio ambiente, sino que también mejoran el manejo mediante el uso de materiales más ligeros y características de seguridad mejoradas”.
En la actualidad, existen muchas tendencias notables y emocionantes en la construcción sustentable, pero una que se destaca para Doka es la reducción del impacto ambiental del hormigón, especialmente sus importantes emisiones de CO2.
Hauser afirma: “Su resistencia, durabilidad, disponibilidad y otros atributos lo convierten en un material de construcción indispensable en la industria de la construcción durante muchos años. Encontrar nuevas formas de hacer que la construcción con hormigón sea más sostenible requerirá la atención seria de todos los actores de nuestra industria”.
Hormigón bajo en carbono
Una opción prometedora, dice Hauser, es el uso de mezclas de hormigón con bajo contenido de carbono, que utilizan menos contenido de clínker pero tienen tiempos de curado prolongados, particularmente en climas más fríos.
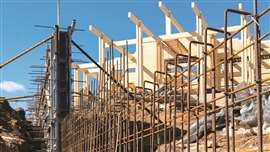
“Este período de curado prolongado plantea desafíos reales en términos de costos y eficiencia, ya que afecta los plazos del proyecto y requiere que el encofrado permanezca en su lugar durante períodos más prolongados.
“Proyectos recientes de investigación colaborativa con líderes de la industria como Strabag y Holcim en Austria buscan desarrollar soluciones que mantengan los estándares de rendimiento del hormigón con bajas emisiones de carbono”.
La contribución de Doka a proyectos como estos incluye el desarrollo de un prototipo de encofrado calentado inteligente destinado a acelerar el desarrollo de la resistencia temprana y facilitar la implementación práctica del hormigón con reducción de CO2.
“Esto incluye el uso de materiales más sostenibles, la reducción de residuos, la economía circular y la minimización de la huella de carbono de los proyectos de construcción”, afirma Hauser.
“Muchas de las soluciones que necesitamos para llegar a cero emisiones netas ya existen, pero otras necesitan ser exploradas e innovadas. Ahí es donde reside el mayor potencial: en entender la sostenibilidad como un catalizador para el desarrollo de nuevos modelos de negocio, productos o servicios”.
De acuerdo con Hauser, está claro que la industria tiene la oportunidad de dar ejemplo en la adopción de prácticas respetuosas con el medio ambiente para el futuro de las cimbras y encofrados.
STAY CONNECTED



Receive the information you need when you need it through our world-leading magazines, newsletters and daily briefings.
CONNECT WITH THE TEAM


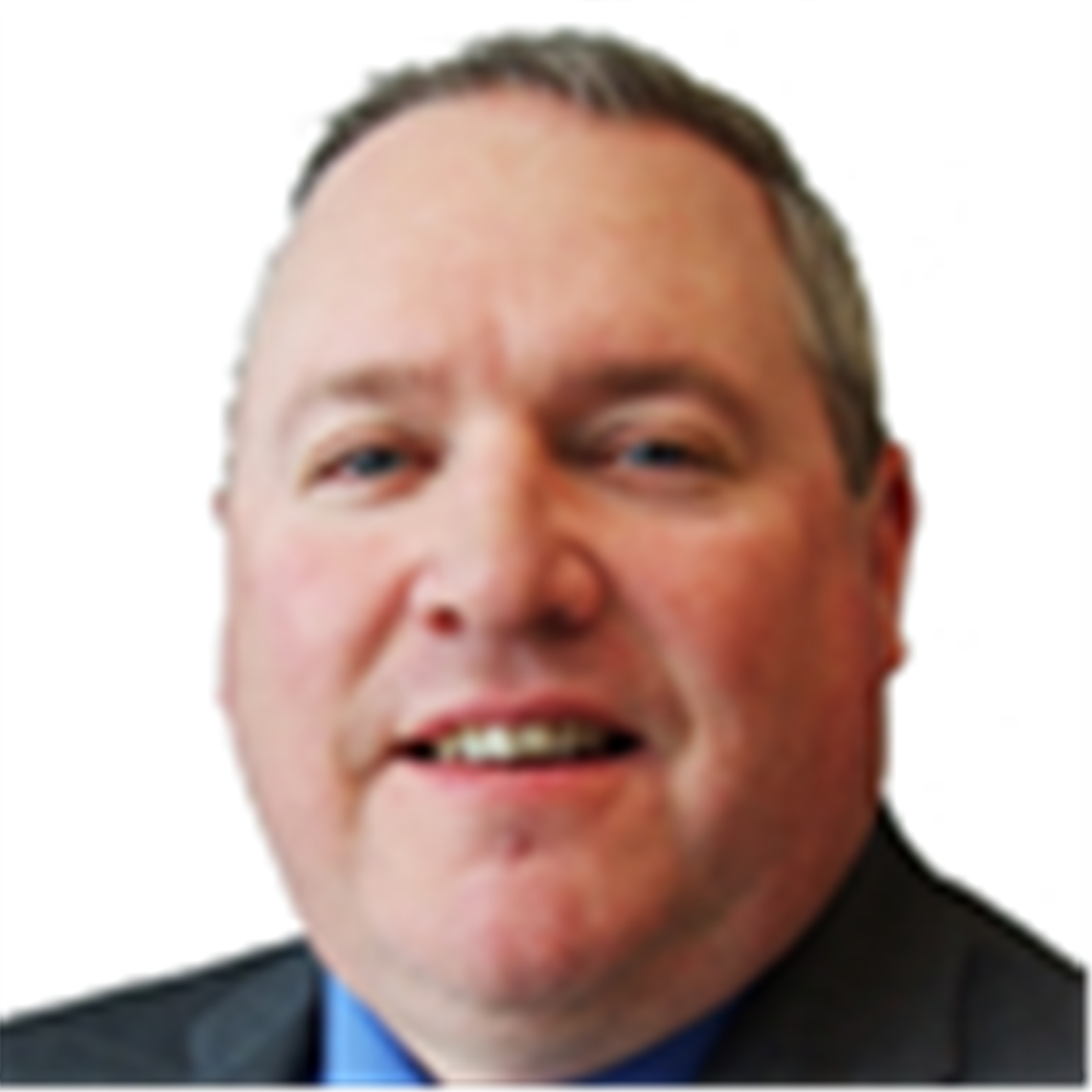
