The fundamentals of safety
12 March 2008
Safety and Training Director with Mastclimbers in Atlanta, Kevin O'Shea highlights some of the important fundamentals to remember when you want to use mast climbing work platforms.
Mast climbing work platforms (MCWPs) are increasing in popularity, and many users, rental companies, owners and safety professionals are looking for guidance on how to safely erect, dismantle and use this highly flexible equipment.
An MCWP is primarily used to position personnel, along with their necessary tools and materials, to perform their work. The two main types of platform currently in use in North America are rack-and-pinion and hydraulic.
MCWPs are very different to other forms of powered access. For example, a scissor lift is delivered from the manufacturer with a fixed load capacity; an MCWP has various load characteristics depending on the configuration of the platform. ANSI A92.9, the current design standard for MCWPs demands that “training on proper use and operation be given upon each delivery by sale, lease or rental.”
The fundamentals
1. The job survey
One of the most important parts of the process, the job survey, occurs before the unit or units arrive at the job site.
The job survey, which should be completed by a competent person, establishes vital information which is used to plan the number and configuration of machines, the method of tying, the ground conditions and the identification of hazards leading to a method statement for the erection and dismantle. It is vital that the person carrying out the job survey has the relevant experience to be able to fully plan a safe installation.
2. Ground conditions
An MCWP 200 foot high can be responsible for 16 tons of load at the ground, or at the point where the base plate or chassis is situated. The ground needs to be solid, flat, compressed and compacted. Danger can arise from underground cavities (which may be dug out after the unit(s) has been erected), such as underground car parks or pipe trenches. The mast, not the chassis or base plate, needs to be absolutely vertical, both perpendicular to, and parallel to the face of the building.
If the unit is being erected on a cantilever bracket arrangement the design must be passed by a qualified structural engineer.
Many people have commented that when they observe an MCWP installation, erectors spend a disproportionate amount of time on the positioning and leveling the unit, and that when the mast erection commences, it goes up quickly. The attention to detail in positioning and leveling can save lives, time and money.
3. What are you tying into?
Ties hold the MCWP, and, therefore, you, to the structure. It is therefore a mystery why very few users pay attention to this critical point. Here is a list of questions you should get answers to before you begin installing expanding anchors into concrete for mast stability:
→ What am I tying into and will it take the loads?
→ What forces (tensile and shear values) need to be counteracted by the anchors or tying system?
→ What size of anchor, and how many do I need?
→ What is the diameter of the hole I need to drill for the anchors, how deep should it be, and how close should the next anchor hole be (the incorrect application of any of these factors can seriously damage the effectiveness of the anchor), and remember to clean out drill holes before inserting the anchor(s).
→ Am I drilling into a post tension slab?
→ What torque setting should be used to tighten the anchors?
4. Tie distance
Make sure you keep within the manufacturer's recommendations on tie distances. One of the common mistakes is to measure the tie distance in “floors” rather than feet. If a manufacturer's guidelines state maximum tie distance 30 feet, most people have the idea that they can tie every three floors. If the floors are more than 10 feet apart you need to get guidance from the manufacturer before tying every third floor.
5. Platform configuration
When building an MCWP, make sure you follow the manufacturer's guidelines on the platform size and configuration.
Experienced installers build the mast first and configure the platform second. This means build the mast with a minimal of platform sections either side of the mast and no unnecessary front edge extensions, these greatly increase the load on the mast and ties.
6. Don't overload the platform during installation or dismantle
Make sure that you only have the recommended amount of mast sections stored on the platform, and that they are evenly distributed either side of the mast, (another reason for minimizing the number of platform sections during erection and dismantle is to physically limit the number of masts that can be stored).
7. Make sure erection and dismantle crews are trained and communicate
Too many times we see properly trained installation crews erecting the MCWPs at the start of the job because the supplier wants to impress, only to see less competent crews brought in for the dismantle phase, or worse, the customer is allowed to dismantle the units, all in the name of economy. This is where accidents can happen.
8. Training
Finally, remember that no one ever got injured because they were over-trained. MCWPs are a fantastic tool, and, when erected and used properly, they can increase safety and productivity simultaneously. Comprehensive training is available and there is no substitute for well informed and properly trained installation and operational personnel in the MCWP business.
STAY CONNECTED



Receive the information you need when you need it through our world-leading magazines, newsletters and daily briefings.
CONNECT WITH THE TEAM


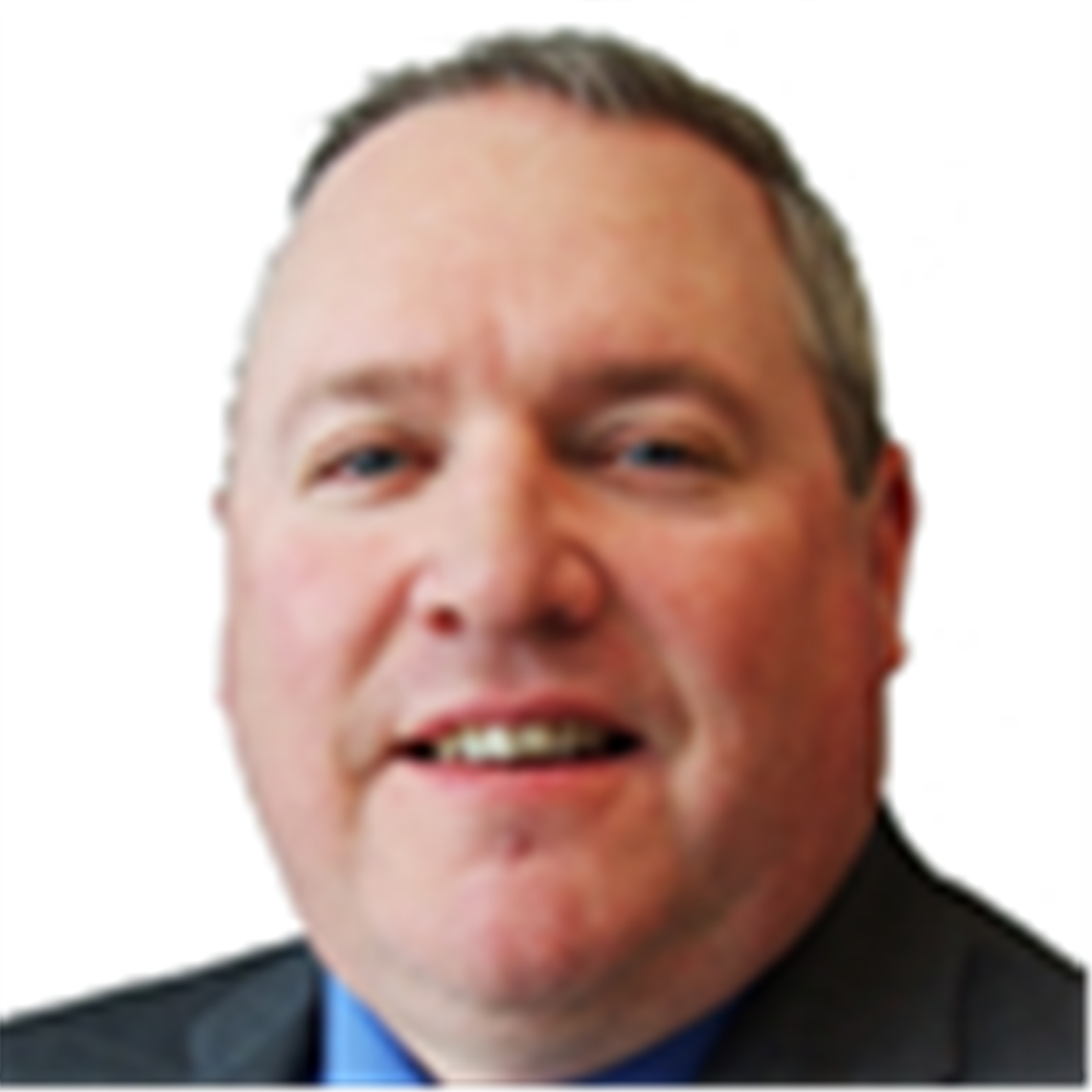
