Infrastructure update: Major U.S. bridge and highway projects in progress
September 05, 2024
Highways and bridges seem to be the infrastructure projects getting the most attention these days. Bridge projects are tedious because oftentimes the new bridge is built while the old bridge is still in use. Highway expansion is the same, with cars whizzing by while construction crews work. Following is ACT’s roundup of infrastructure jobs currently in progress around the country.
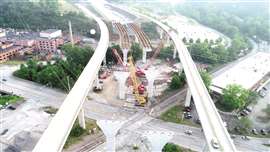
Down the ‘Pike
State officials in Pennsylvania have known for years that there’s no easy way to get from Uniontown to Pittsburgh to the north. Now, the Turnpike Commission is addressing the need with a new high-speed bypass. The commission’s Mon-Fayette Expressway (PA Turnpike 43) project is four projects in one, the first three having been built and stretching 54 miles by connecting I-68 near Morgantown, WV to PA Route 51 in Jefferson Hills, PA.
A recent operation required two lattice-boom crawler cranes to set beams over Route 51 to construct a new bridge. ALL Crane Rental of Pennsylvania, a member of the ALL Family of Companies, supplied a pair of Manitowoc MLC300 crawlers to dual-pick the beams for the job, overseen by its customer Century Steel Erectors of Dravosburg, PA.
The MLC300s were chosen for their capacities as well as the ease with which they can move to different set-ups on the jobsite. Each crane was configured with Series 3 counterweights at 474,000 pounds and 177 feet of main boom. They were used to lift a series of bridge beams ranging in length from 134 feet to 150 feet and weighing up to 90,000 pounds.
“At times, we were lifting doubles,” said Billy Rieger, dispatcher for ALL Crane Rental of Pennsylvania, “which increased weights to 180,000 pounds.”
For the dual picks, each crane hooked to rigging attached to carefully planned pick points, lifted each piece 98 feet in the air and brought them to rest on bridge piers where Century Steel’s ironworkers could complete tie-ins. It took approximately two hours to accomplish each lift, with 16 beams set over four 10-hour days. Also assisting with the lifts was Century Steel’s own 250-ton capacity crawler crane.
Although the cranes were set up in such a way that the booms extended between existing bridges on either side, Rieger said the site was well-prepared and there were no obstruction issues or challenges.
For this first portion of the bridge work, no road closures were required as it is new construction. However, connecting spans will eventually put the work directly over Route 51 below. At that time, Route 51 will be closed for a weekend as the spans are connected. Work will likely go on around-the-clock to ensure it is completed in the allotted time.
The next portion of this project will see bridge construction over Coal Valley Road. Rieger anticipates the two MLC300 crawlers will be used for that work as well.
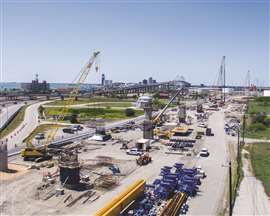
Huge hoisting
At the $1.2 billion Harbor Bridge project, which will span the Corpus Christi Ship Channel, the contractor needed a crane capable of hoisting heavy box girders that weighed more than 100,000 pounds.
Bigge Crane & Rigging dispatched its Liebherr LR 1750 to the jobsite. The 800-ton capacity crawler crane was configured with 207 feet of main boom and 92 feet of luffing jib.
“The impressive lifting power of this crane and its adaptability made it the perfect choice to support the long-term project of replacing the existing Corpus Christi Harbor Bridge, enabling larger vessels to access the port,” said Bigge’s Joe Nelms.
Protecting the coastline
The Lower Manhattan Coastal Resiliency (LMCR) Project is an integrated coastal protection initiative aimed at reducing flood risk due to coastal storms and sea level rise in Lower Manhattan. It will span the Lower Manhattan coast and seeks to increase resiliency while preserving access to the waterfront and integrating with public space, mainly parks. The city, state and the federal government have committed over $1.7 billion in capital investments for the coastal protection projects.
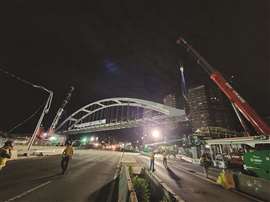
Bay Crane was recently involved in the one of the projects, erecting a pedestrian bridge over FDR Drive in Lower Manhattan. This is the first of three bridges that Bay Crane will help erect.
Using the Accelerated Bridge Construction (ABC) process, the bridge was built about a mile south of the erection location. Using a six-line SPMT system, Bay Crane transported the bridge system to the jobsite.
Two of Bay Crane’s Liebherr LTM 1450s were dispatched to the site and set up adjacent to each other and perpendicular to the viaduct. The bridge weighed 365,000 pounds and was 212 feet long. It measured 19 feet wide and was 34 feet tall.
“The two cranes were rigged the same with 295,000 pounds of counterweight on each machine,” said Bay Crane’s Mike Catik. Two 19-foot, 200-ton spreader bars were used on each crane to grab the ends of the bridge and lift them in place.”
The job was done at night and required the full closure of FDR Drive. Bay Crane worked directly for the NYC Department of Design and Construction and Tri Venture. Bay Crane also worked in tandem with the steel erector, American Structural Works and the local Ironworkers.
Overpass replacement
Lane Construction Corporation is building two bridges over the Wateree River in Kershaw County, South Carolina. The bridges will replace two existing overpasses along Interstate 20 as part of a South Carolina Department of Transportation bridge rehabilitation project.
Lane’s scope of work includes the demolition of the old structures, which were built in the 1970s, the construction of the new bridges, and rehabilitation work on two additional pairs of I-20 overflow bridges built in the 1970s. The company will also complete approach roadway work to incorporate the new bridges into I-20.
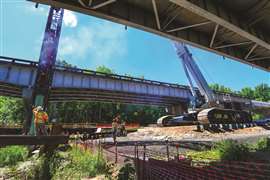
Lane is utilizing two Link-Belt 250-ton TCC-2500 telescopic crawler cranes on rent from Lomma Crane & Rigging of Bridgeville, PA. Lane first used the TCC-2500s to drive piling to build temporary trestles on both sides of the river. As the river is a navigable waterway and requires maintained access through its middle, the Lane work crew is using the TCC-2500s concurrently, one on each trestle, to begin foundation work for the replacement bridges.
Although a traditional lattice boom crane was used to start the project, Lane Project Director Eric Pruemer realized it was not optimized for the tight, confined jobsite. He said the TCC-2500s were needed to do the job right.
“These allow us to easily go underneath the bridge back and forth to facilitate work on both the outside and the median of this bridge,” Pruemer said.
The cranes’ ability to quickly retract and extend their booms mean they can travel under each bridge and work on either side when driving the steel tubular pile needed to construct bracing for the existing bridges throughout the demolition process.

Cincy bridge
Maxim Crane Works dispatched two cranes to perform the tandem pick to place a pipe bridge on the Mill Creek Bridge Project. The bridge will hold a pipe that will carry water for Cincinnati Water Works.
The two cranes were a Liebherr LTM 1650-8.1 and Grove GMK7550. The bridge weighed approximately 132,000 pounds and was 207 feet long.
The cranes were set up on each side of Mill Creek. Ground preparation included leveling, shoring and creating a sturdy gravel base.
Trestle upgrade
The 43-year-old I-494 bridge over the Minnesota River (and directly southeast of the Minneapolis-Saint Paul International Airport) needs major repairs to continue to safely transport people and goods between the cities of Bloomington, Eagan and Mendota Heights, MN.
In 2023, Black River Falls-based Lunda Construction was awarded a $62 million contract to repair the bridge, including pavement repair, reconstruction of a regional trail, replacement of bridge joints, repairs to the bridge deck and railings, reconstruction of bearings, replacement of highway lighting and drainage repair.
The I-494 steel girder bridge over the Minnesota River bridge is 4,502 feet long with 37 spans. Lunda is repositioning all bearings on the expansion piers and replacing rocker bearings on the steel spans. The bridge decks are 60 feet wide with a typical concrete girder span of 114 feet long and 200 feet steel span, with the longest span of 260 feet.
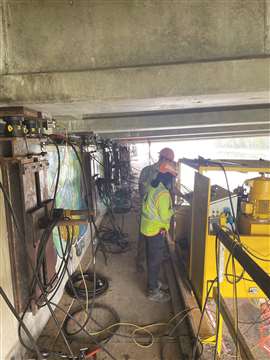
The solution for the project is an Enerpac EVO Series Synchronous Lifting System based on Enerpac’s computer control technology. The EVO provides easy set-up and control for 4, 8 or 12 lifting points per pump. There are multiple lifting options. Pump units are available with several flow options for optimal lifting speed, as well as built in warning and stop alarms for optimum safety. Multiple pumps can be networked together to control up to 48 total lifting points from a single operator control station.
At the bridge project, the EVO was configured with two LPL-602 cylinders per control point. The 12 pair of cylinders are arranged in two rows of 12 lifting points on top of the pier. The typical lift at each beam end reaction is a dead load of 154 kips.
The first step on preparing the bridge pier for the installation of the jack bracket system is coring through the pier cap to enable post-tensioning threaded bar installation. Once the brackets are hung on the cap, the threaded bar is stressed to a range of 265 to 280 kips. With the brackets stressed, the Enerpac cylinders are set onto the brackets and shimmed level. A bearing plate is installed between the cylinder and bottom of the steel girder, after which cylinders are ready to be hooked up to the Enerpac EVO system and lifted.
In most cases the Enerpac LPL cylinders are jacked up a half inch, however for certain repairs such as rocker bearing replacements, the bridge is lifted higher for more room to work. Once fully jacked, the Enerpac LPL cylinders are locked allowing bearing replacements, concrete surface repairs on the pedestals and painting of the bearing and sole plates. The longest a span has been jacked and held by the LPL cylinders is 2.5 weeks.
“The Enerpac EVO system has been extremely beneficial for this project,” said Max Byzewski, project engineer, Lunda Construction. “The deck does not have much flexural capacity, so it is critical that each girder on a given beam line is lifted in-sync. The EVO system also has the ability to tell us how much load each jack in a line is experiencing, which shows which girders are seeing more load. This in turn helps better understand why certain girders aren’t coming up as easy as others – namely fascia and center girders.”
The other crucial EVO feature is the pump’s ability to read stroke sensors, allowing the computer to read exactly how high each girder has been lifted, as well as controlling the pressure in each jacking cylinder to ensure a synchronous lift. This avoids the need for Lunda engineers to hard measure each beam, the EVO pump does it for them.
“The most challenging part in this type of bearing replacement project is getting everything set-up,” Byzewski said. “The lift becomes very easy with the Enerpac EVO system where the synchronous nature of the lifts is critical due to low flexural capacity in the deck.”
STAY CONNECTED



Receive the information you need when you need it through our world-leading magazines, newsletters and daily briefings.
CONNECT WITH THE TEAM



