Old Parkland Bell Tower project snags SAIA award
February 28, 2022
The Scaffold & Access Industry Association (SAIA) presented the 2021 Mast Driven Hoists and Platforms Project of the Year Award to Mdm Scaffolding Services, Inc. for the Old Parkland Bell Tower Project. The collaborating company was D.H. Charles Engineering, Inc.
Companies in construction, along with their estimators, field crews, and engineers, were constantly brought into complex challenges that they were not prepared for during 2020, the year of the pandemic. As the country began to shut down, Mdm Scaffolding Services, Inc. and D.H. Charles Engineering were fortunate enough to receive calls from one of Mdm’s top general contractors and masonry contractors for a new iconic structure that was coming to downtown Dallas.
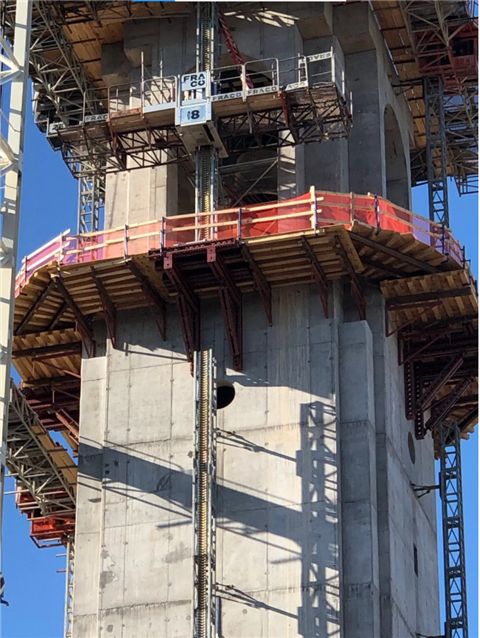
The Trammell Crow Development company was adding to their Old Parkland office campus by constructing a new bell tower to house the fourth largest bell in North America, The bell is 9 feet in diameter, weighs over 30,000 pounds and is named Horatio. It is now housed 220 feet high in a structure that stands 40 feet by 40 feet and over 280 feet tall, located at the main entrance of the campus.
The Bidding Phase
During the bidding phase Mdm was called on by multiple masonry contractors to help design exterior access from the base of the tower around the perimeter all the way up to access the dome and the spire. The structure alone is a fairly simple design with the largest length of only 40 feet, but Mdm was being asked to help the masons hit a very aggressive schedule. The scope of work called for 75 days for installing stone to the entire exterior and providing access for the waterproofing, electrical, masonry and roofing contractors to access the tower, dome and spire safely. Each mason had their ideas of how they wanted to attack the structure, but whoever came up with the most creative design was winning this project. One of Mdm’s top masonry customers is a large Fraco user and knew about the ability to “double stack” their projects, by providing a single mast unit that allowed crews to work on multiple decks at the same time - but that still wasn’t the total solution.
Mdm reached out to key members of the Scaffold & Access Industry Association (SAIA) and worked closely with D.H. Charles Engineering, Mastclimbers LLC, and Fraco to see what had been done in the past. They also discussed current ideas that might be possible. Mdm reviewed multiple different projects around the nation and overseas and came up with a three-tier concept design that would allow all four sides of the structure to be worked on at three different levels. The concept involved a structure that the Mdm team called a “chair stand.” At the same time, they believed that this had never been done before and weren’t sure if it would work mathematically.
Chair Stands
Mdm approached D.H. Charles with a cantilevered mast climber projects that were successfully done before and their new concept. The chair stands would be located at two different elevations and each mast clumber would be based on top of them and anchored into the structure. The main approach was to use typical components and not have to fabricate custom components, which would keep overall costs and timing down.
Rising to the task, D.H. Charles used typical components to develop a conceptual design based on the current estimated loads for each mast-climber location. Based on their work, Mdm provided the customer and general contractor hybrid 3D designs that included 16 Frace ACT8 mast climbers, eight chair stands, 40 bridge overhang brackets and a full dome wrap utilizing Ringlock scaffolding
The Engineering Process
From the bidding process, both Mdm and their masonry customer were awarded the project, and the long engineering process began with the most crucial part of the project, the chair stands. The chair stands were the ultimate reason why the mason was able to win the project and meet the aggressive schedule
D.H. Charles engineered the chair stands to use Dayton Superior soldier beams with steel rods and plates secured to the structure. Each chair stand was designed to handle 43,000-pound loads being pressed through the individual masts of the mast climbers. D.H. Charles utilized typical bridge overhang brackets that provided 8 to 10 feet of overall coverage below each of the two raised levelers of mast climbers. This overhead protection (OHP) made it possible for three different elevations to be worked at a single time. The OHP deck also doubled as a safe landing for personnel and some materials as it had guard rails on all four sides of the tower.
Considering how complex the conceptual designs were, the actual back and forth between the Engineer of Record (EOR) and D.H. Charles was very smooth. The structure was designed so stout that it was a much simpler review process than anyone anticipated. The Mdm team believed that using the cantilevered chair stands along with the double-stacked units was the first design of its kind.
Time-Saving Design
The dome access added another complex aspect to the project that required D.H. Charles and another engineering firm to work together. Mdm worked with both the general contractor and the mason to modify the initial dome scaffold design and reduce the overall transition time from the dome scaffold to the mason scaffold. The initial plan was based on Mdm’s budget design in which the dome scaffold would be installed first and then removed. Then the new masonry-style access would be installed to do the remaining brick and stone installation. Mdm came up with a new concept design that allowed the masonry style scaffold to be installed first and the dome access scaffold second.
Mdm called on D.H. Charles and Fraco to see if their new concept was even feasible and if both firms would be willing to take on the new design. D.H. Charles agreed to provide engineering and stamp for the scaffolding, point loads and the distribution of the point loads based on the equipment guidelines. Fraco provided a professional engineer consultant who signed off on the loads being distributed over the Fraco decking, which would allow Mdm to base all their equipment off the decks and to cut the equipment needed and the durations in half. Mdm installed all the cantilevered bases and decking and their mast climbers at the third level below the dome. Then they locked out most of the mast climbers just below the bottom of the dome and tied them in. Once this was completed, Mdm flew all their equipment up on tip of the mast climber decks. The equipment included components for an approximately 30-to-40-feet-high scaffold to provide a four-sided, fill scaffold wrap with multiple deck levels for dome and spire access.
Installing the masonry equipment and basing off the existing decks eliminated any down time on the mason’s part, and the project gained some three to four weeks on the schedule. The scaffolding being cut in half reduced the install by about a week and reduced the overall dismantle down to four days. Once the final piece of Ringlock was removed, the mason was immediately able to begin flying in their large stone pieces for the archways. The mason finished their portion of the exterior schedule with a two-to-three-week cushion on the general contractor’s schedule.
Early Collaboration
Old Parkland Bell Tower Access was a one-of-a-kind mast and scaffold design that consisted of a stacked mast configuration to maximize masonry efficiency, cantilevered modular scaffold built on top of the masts. Significant coordination was required by Mdm, the mason, D.H. Charles Engineering, the EOR and the third-party mast engineer to determine what was required. This project is a great reference for how scaffolding companies are taking new steps to work closer with not only their customers but also the engineers and general contractors, starting as early as the budget phase.
STAY CONNECTED



Receive the information you need when you need it through our world-leading magazines, newsletters and daily briefings.
CONNECT WITH THE TEAM



